What is EMI?
EMI, otherwise known as Electromagnetic Interference, is an unintended digital “noise” or frequency that disrupts the electrical path of a nearby electronic device. EMI can be created by both natural and man-made means, and is caused, on some level, by all electronic devices. Electronic devices, when powered on, will emit a magnetic field, and begin radiating electromagnetic waves. Whenever two or more electronic signals meet at the same frequency, they disrupt one another, causing EMI. EMI interferes with the intended frequencies and reduces the overall signal quality. EMI can cause electronics to function poorly, or completely render them inoperable. Some examples of EMI are: the beeps and noises heard when a cell phone is placed near a speaker, microwave ovens that disrupt nearby WIFI networks, or, as in the case of an LCD; EMI can appear as snow and static, a discolored display, or a blank screen. EMI also has natural causes, like static electricity, lightning, and even the Earth’s atmospheric Aurora phenomenon. EMI is also commonly referred to as Radio-Frequency Interference (RFI).
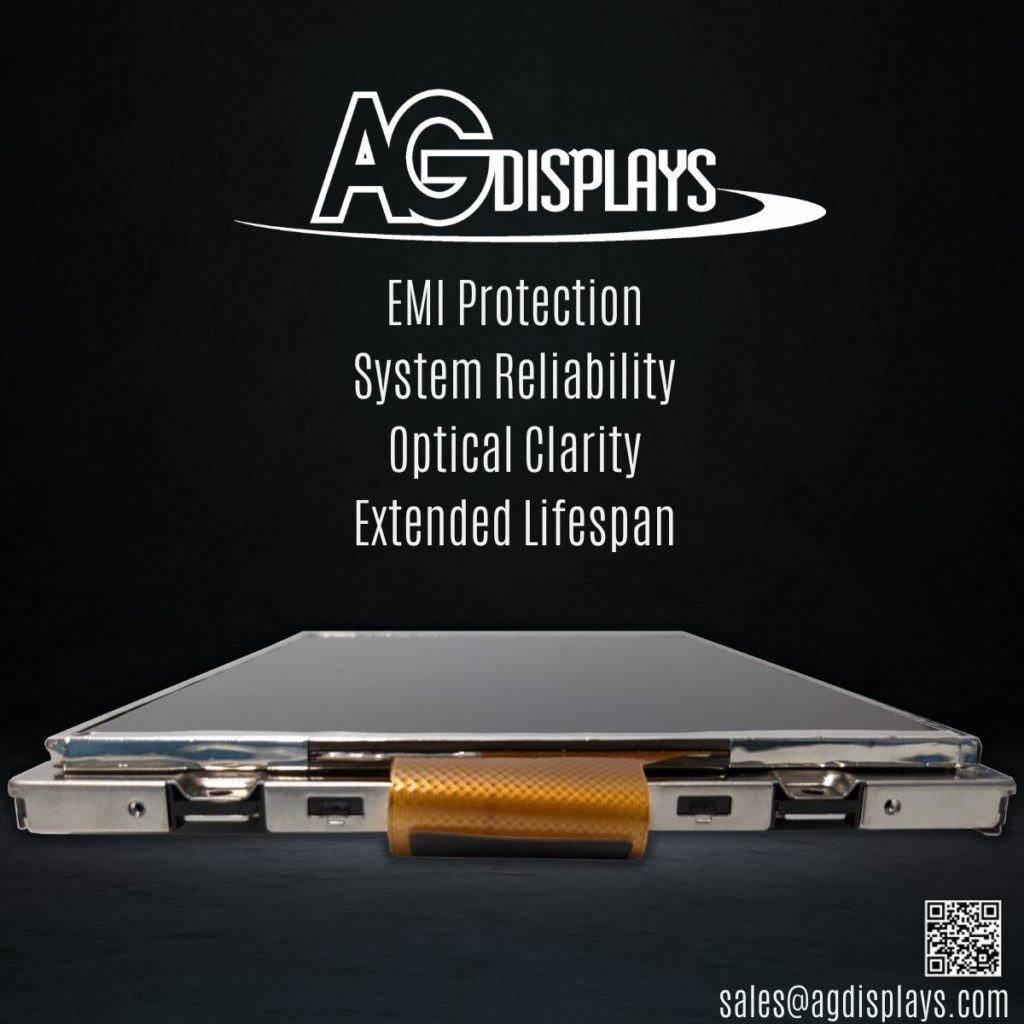
Types of EMI
There are two main types of EMI based on how the interference is transmitted.
Conducted EMI
Conducted EMI comes from two or more electronic devices in physical contact with one another. In this example, physical contact can come from two or more items using the same electrical circuit (such as multiple devices plugged into a power outlet). EMI can be seen in this scenario when using one of the devices causes another connected device to malfunction.
Radiated EMI
Radiated EMI is a more common form of EMI and is created by two or more electronic devices without the need for direct contact. The EMI in this in this case is thus transmitted wireless and can travel to nearby devices without the need for a direct electrical connection.
What Causes EMI in LCD Displays?
EMI, in relation to LCDs and touch screens, often comes from the components used to assemble the display. LEDs, controllers, cabling, power supplies, and front of the display can all emit their own levels of interference. To prevent EMI from spilling into the environment, display internals are usually contained within a metal backplate acting as a faraday cage. LCD modules and components are at many times grounded via DC ground, while cables and power supplies are shielded with ferrite or copper protection.
Why is EMI Protection Important?
EMI protection and EMI shielding are important due to the fact that in many highly technical and critical applications, such as medicine, military, and aerospace, many small and powerful electronic devices are often used together, in conjunction and in close proximity. In the worst-case scenario, interference by one of these components can create a total system failure.
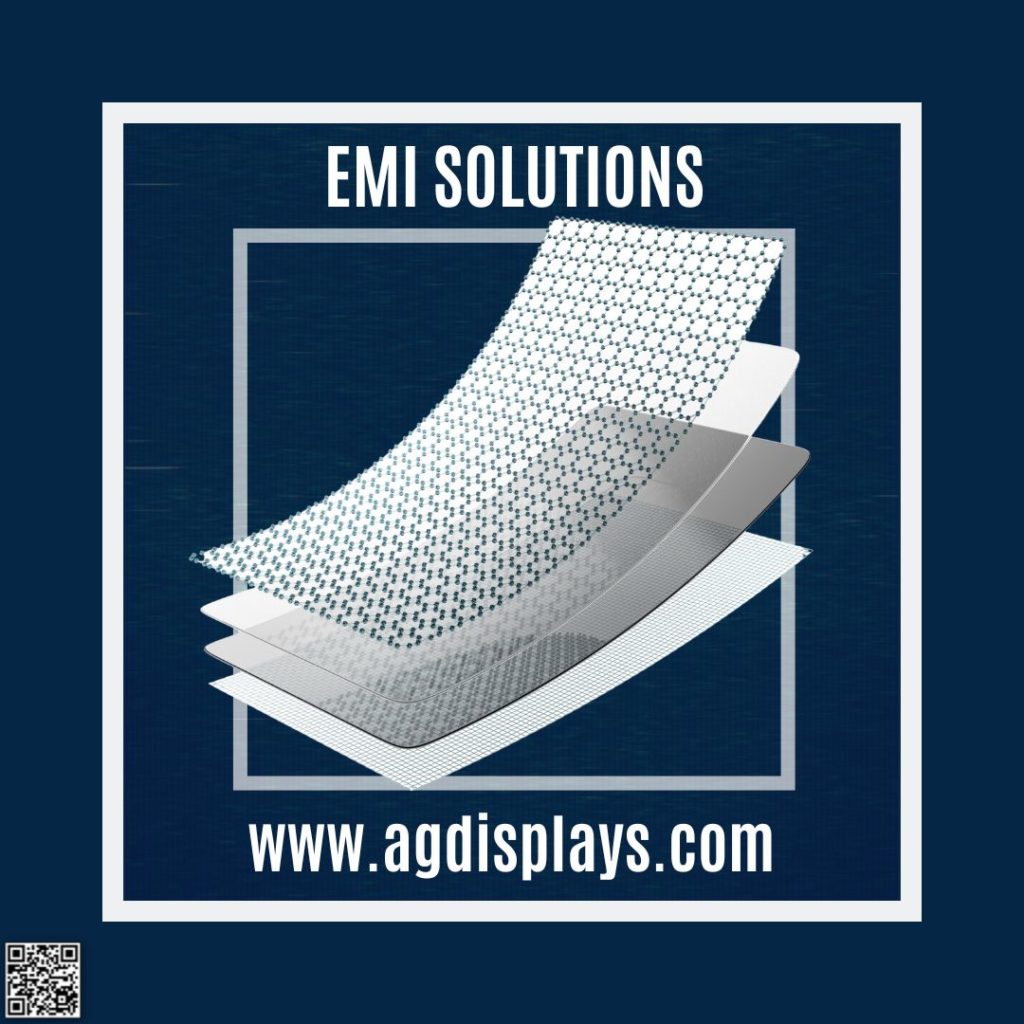
How does EMI Effect a PCAP Touch Screen?
Projected Capacitive (PCAP) touch screens are inherently sensitive to EMI. A PCAP functions by using a conductive grid that recognizes changes in its electromagnetic field by the touch of your finger. The changes in the electromagnetic field are measurable by an electronic touch screen controller, which then processes the measurement and converts it to a position on screen. Disturbance by EMI can disrupt the PCAPs electromagnetic field and cause false touches and failed touch screen response. Common sources for EMI related to PCAP touch screens mainly come from the LCD, as the PCAP touch and the LCD are bonded with just a few millimeters between them. EMI affecting the PCAP can also come from nearby exposed wiring or controllers, and from handheld and mobile devices and chargers used near the touch screen. EMI can also come conversely from the PCAP itself, and effect nearby electronic equipment.
Types of EMI Protection
Controller Tuning
When the issue causing the EMI is related to the LCD, or another known source (such as WIFI or radio equipment), it’s possible to take this into account and make adjustments within the touch screen controller software. This method is usually the quickest and easiest way to reduce PCAP noise and EMI malfunctions, because it requires no additional hardware and can often be performed on-site or via wireless update.
EMI Mesh
EMI Mesh is a common method of mitigating the effects of EMI, and in general terms, is a “highly conductive series interlocking strands of either steel or copper wire”. The material can be either knitted or woven, allowing for more flexible or rigid constructions alternatively. EMI Mesh is specified in terms of material, wire treatment, count (opi) and thickness. EMI Mesh is laminated to the PCAP touch screen and encapsulated using clear adhesive substrate, so that no air gaps are present, and the lattice structure of the EMI mesh is not exposed. Special consideration is also taken so that any exposed areas of the display do not act as an antenna for EMI to travel towards. EMI mesh is used to provide high levels of EMI shielding, while maintaining the optimal brightness and clarity of the display.
ITO Coatings
ITO or Indium Tin Oxide, is used in PCAP and LCD applications to make transparent conductive coatings that help to deflect electromagnetic radiation. When combined with laminate materials such as a flexible polyester, or a more rigid material like glass or acrylic, ITO layers can be a quick solution to Electromagnetic Interference problems. ITO coated layers provide rugged enhancements that can be fully laminated with a given surface finish requirement, and bonded to the display, providing both EMI and environmental hazard protection.
Solid and Flexible EMI Shielding
EMI Shielding is used to reduce the total EMI noise over the entire display module and commonly includes fabricated metal sheets made from aluminum, copper, or steel. EMI shielding reflects electromagnetic waves in to the display housing, and absorbs the remaining waves that are not reflected in.
Flexible shielding is created from particle-filled silicone used in place of rigid metal, and is used for gasketing and sealing in environments where solid metal could contract and expand. While pure silver was once the particle additive of choice, due to rising silver costs, alternative particulates are generally used, such as silver-aluminum, silver-glass, and nickle-graphite.
EMI Tape
Conductive EMI tape is a quick and economical solution to solving undesirable EMI problems. Copper tape is often used to seal the edges of a display and act as an electrical enclosure like a faraday cage. Conductive tape is perfect for filling in gaps and seams between an LCD and PCAP touch, and can be laser cut to match the exact dimensions of the display. Most conductive EMI tapes consist of copper or Amurcor foil along with an adhesive later. Some tapes will also include an insulation layer, or instead of foil, will be made of a more elastic textile tape.
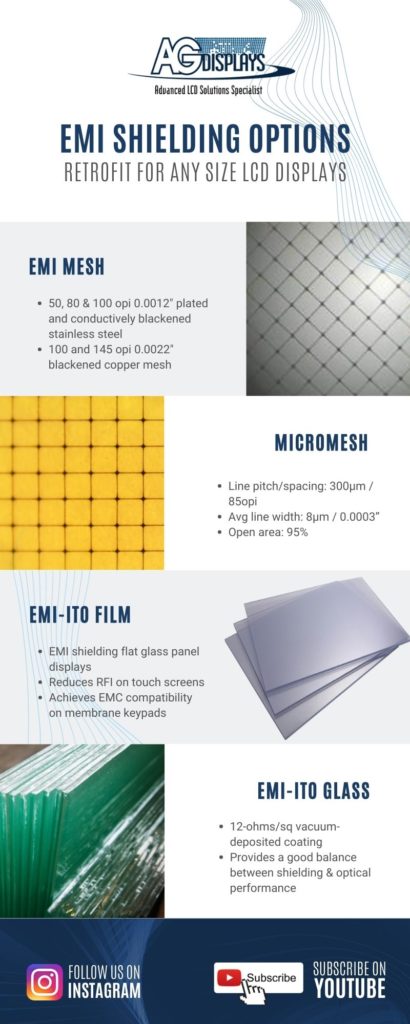
AGDisplays Preferred EMI Solutions
EMI Transparent Thin-Film Conductive Coating
Transparent thin-film conductive coatings provide LCD technology with great optical and EMI shielding properties. Some films contain layers of indium tin oxide (ITO) and metal alloy films. By increasing the conductivity of the coating, the EMI attenuation level average will increase. Typically the frequency level ranges in 100 kHz – 20 GHz. Films may be offered with conductivity ranging from 1 to 100 Ω/sq. Film solution provided for panels needing low attenuation (10-30 dB)
- Our EMI solution is a transparent conductive film
- Cost effective solution, not involving an active enhancement
- Compatible for use with a touch sensor
- High visible transmission with low electrical resistance:10 and 20 ohms/sq
- Significantly reduces problematic EMI and/or IR emissions from surface
- Superior to ITO films at low resistance for transparency & mechanical properties
Conductive Grid Mesh Solution
Conductive grid mesh solutions provide panels a high level of protection. A fine-conductive grid may be built of woven stainless-steel or copper mesh, or alternatively made with a patterned conductive metal coating on the substrate’s surface.
- Woven wire mesh
- Robust active enhancement, providing high level of protection
- Compatible for use with a touch sensor
- Photopic transmission at ≥85%
- Diffuse reflectance at 30° at ≤0.14%
- Specular reflectance at 30° at ≤1.2%
- ≤0.25 Ω/sq. surface resistance
- Shielding effectiveness: 50Mhz (megahertz):~75dB or 100Mhz:~65dB
Visit our Shopify Store: shop.agdisplays.com