Liquid Crystal Displays (LCDs) are a cornerstone of modern technology. From smartphones to automotive dashboards, televisions, and medical devices, LCDs are integral to daily life. Yet, as demand for these displays grows, so does the environmental toll of their production. Energy-intensive manufacturing processes, reliance on scarce materials, and significant waste generation have made sustainability an urgent priority.
In the face of climate change, resource depletion, and consumer demand for eco-friendly products, the LCD manufacturing industry must evolve. This blog delves into the environmental challenges, groundbreaking technologies, economic trends, and real-world success stories that are shaping the future of sustainable LCD manufacturing.
Environmental Challenges in LCD Manufacturing
Material Sourcing
LCD manufacturing depends on materials like indium tin oxide (ITO), liquid crystals, polymers, and glass substrates. Extracting and refining these resources is both energy-intensive and environmentally destructive:
- Indium Dependency: Indium is a rare metal sourced as a by-product of zinc mining. Its limited availability and high extraction costs pose challenges to sustainability.
- Resource Depletion: Large-scale mining operations for materials like quartz for glass substrates can lead to habitat destruction and biodiversity loss.
Energy Consumption
The manufacturing process for LCDs includes steps like substrate preparation, chemical vapor deposition, and cleanroom operations. Each step requires significant energy input, much of which is still derived from non-renewable sources. This contributes directly to greenhouse gas emissions and climate change.
Chemical Usage and Waste
- Toxic Chemicals: Production involves hazardous substances like etchants, photoresists, and cleaning solvents, which are difficult to dispose of safely. Accidental leaks or improper disposal can devastate ecosystems.
- Manufacturing Waste: Defective panels and off-spec materials often end up in landfills, contributing to the growing global e-waste problem.
Water Usage
Water is critical in LCD production, especially for cleaning and chemical dilution. Traditional manufacturing processes consume vast amounts of water, leading to waste and pollution in regions where resources are already scarce.
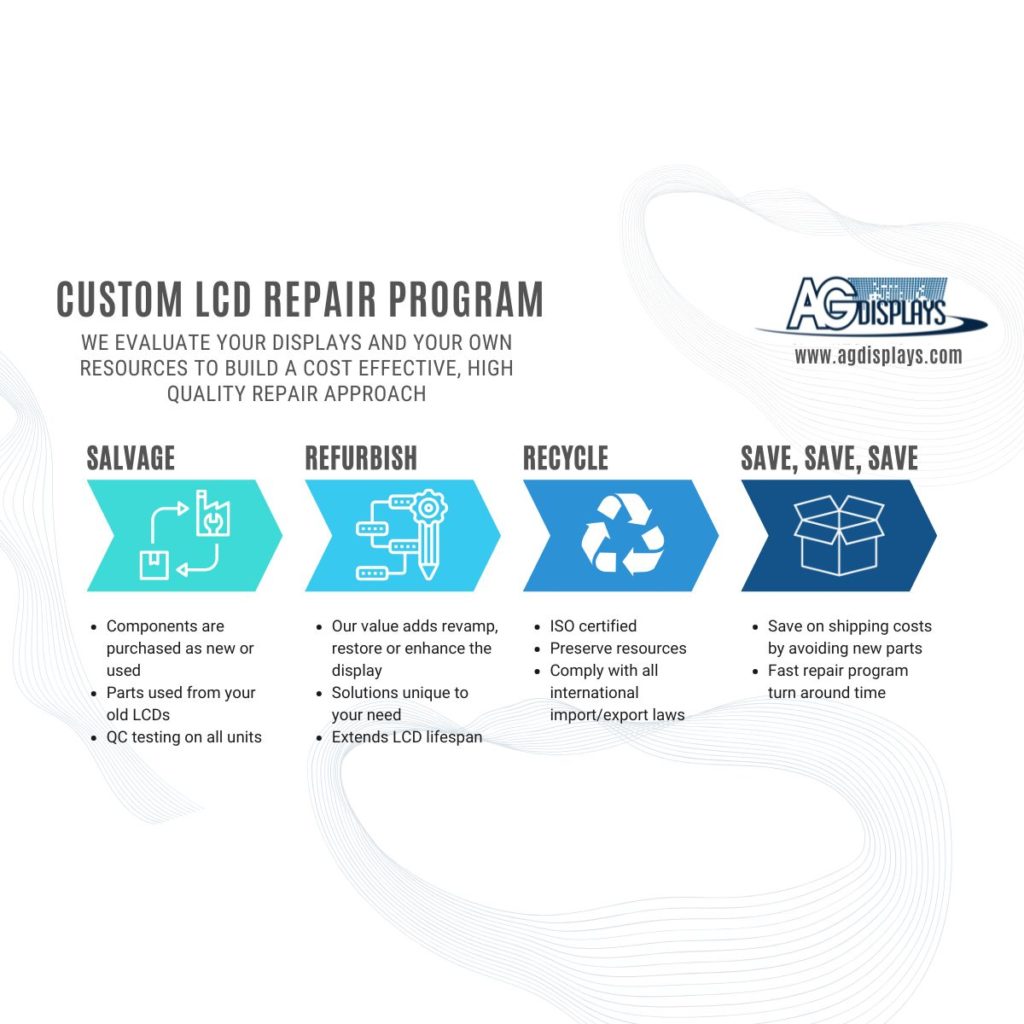
Innovations in Sustainable LCD Manufacturing
Recycled and Bio-Based Materials
Manufacturers are incorporating recycled glass and polymers into LCDs, reducing reliance on virgin materials and lowering their carbon footprint. Bio-based polymers derived from renewable sources like algae and cornstarch are being tested as replacements for petroleum-based plastics.
Energy-Efficient Processes
- Low-Temperature Processing: Techniques like Low-Temperature Polysilicon (LTPS) allow manufacturers to produce high-performance displays with less energy.
- LED-Based Photolithography: This newer method consumes significantly less power compared to traditional photolithography, while also extending the lifespan of production equipment.
Water Recycling Systems
Closed-loop systems allow manufacturers to treat and reuse water within the production cycle, saving millions of liters annually and preventing wastewater discharge.
Non-Toxic Chemicals
Researchers are replacing hazardous substances with eco-friendly alternatives, making production safer for workers and less damaging to the environment.
Emerging Green Technologies in LCD Manufacturing
As the LCD industry seeks to reduce its environmental footprint, emerging green technologies are driving transformative changes. These innovations address energy efficiency, material sustainability, and recyclability, paving the way for a greener future.
Quantum Dot Technology: A Game-Changer for Efficiency and Color Accuracy
Quantum dots are nanoscale semiconductor particles that emit light when exposed to energy. Their application in displays has significantly improved energy efficiency and color performance.
- Energy Efficiency: Quantum dots require less backlight energy compared to traditional LCDs, reducing power consumption by up to 30%. This is particularly valuable in high-resolution displays used in televisions, monitors, and mobile devices.
- Environmental Benefits: Traditional phosphor materials in displays often contain toxic substances, such as cadmium. Cadmium-free quantum dots have emerged as a safer alternative, ensuring compliance with environmental standards like the European Union’s Restriction of Hazardous Substances (RoHS) directive.
- Real-World Adoption: Companies like Samsung and TCL have already integrated quantum dot technology into their QLED (Quantum Dot Light Emitting Diode) televisions, achieving vibrant colors with lower energy costs.
Transparent Conductive Materials (TCMs): Reducing Rare Earth Dependency
Indium tin oxide (ITO), a widely used material in LCDs, is both expensive and environmentally challenging due to the scarcity of indium. Emerging alternatives offer sustainable and cost-effective solutions:
- Graphene: This carbon-based material is incredibly lightweight, flexible, and conductive. Graphene’s abundance and recyclability make it a promising substitute for ITO in transparent electrodes.
- Carbon Nanotubes: Similar to graphene, carbon nanotubes provide excellent electrical conductivity and transparency. They are particularly suitable for flexible displays, opening up new possibilities for foldable and rollable screens.
- Silver Nanowires: These are being explored for their potential to replace ITO in applications where conductivity and optical clarity are critical. While silver is less abundant, its use in nanowire form reduces material requirements significantly.
These alternatives are easier to recycle than ITO, improving the overall lifecycle sustainability of LCDs.
OLED and Hybrid Displays: Balancing Sustainability and Performance
Organic Light Emitting Diode (OLED) technology is often viewed as a sustainable alternative to LCDs. However, the combination of OLED and LCD technologies into hybrid displays is providing the best of both worlds:
- Advantages of OLED: OLEDs do not require a backlight, reducing energy consumption. They also use fewer layers, leading to thinner and lighter designs.
- Challenges: While OLEDs are more energy-efficient during use, their manufacturing process is complex and involves materials that are not easily recycled.
Manufacturers are developing hybrid displays that combine LCD backlighting with OLED-like efficiency and image quality. This approach offers an eco-friendly solution for applications requiring high brightness and durability, such as outdoor screens.
Recycled and Bio-Based Polymers: Rethinking Material Inputs
- Recycled Plastics: By incorporating post-consumer recycled plastics, manufacturers can reduce their reliance on virgin materials and cut greenhouse gas emissions.
- Bio-Based Polymers: Derived from renewable resources like cornstarch, cellulose, and algae, bio-based polymers are biodegradable and significantly reduce the carbon footprint of LCD components.
Companies like Corning, a leading glass substrate manufacturer, have explored blending recycled glass with bio-based polymers for display panels, ensuring durability while prioritizing sustainability.
Low-Temperature Manufacturing Processes: Cutting Energy Usage
LCD manufacturing typically requires high-temperature processes, contributing to energy consumption. Innovations in low-temperature manufacturing aim to address this issue:
- Low-Temperature Polysilicon (LTPS): LTPS processes enable the creation of high-performance displays at lower temperatures, reducing energy requirements by up to 20%.
- Cold Spray Coating: This technique allows the application of conductive materials without heating, eliminating the need for energy-intensive thermal processes.
These methods lower operational costs, extend equipment lifespans, and reduce greenhouse gas emissions.
Advanced Recycling Technologies: Closing the Loop
Recycling has always been a challenge for LCDs due to the complexity of separating components. Emerging technologies are making it more feasible and efficient:
- Hydrometallurgical Processes: These involve the use of liquid solvents to recover valuable materials like indium and rare earth metals from LCDs. The efficiency of these processes has improved dramatically, with recovery rates exceeding 90%.
- Pyrometallurgical Recycling: This method uses high heat to break down displays and extract metals and other components. It’s particularly effective for recovering rare and expensive materials.
- Automation in Recycling: Robotic systems are now being used to disassemble LCDs automatically, ensuring precision and reducing labor costs.
Flexible Displays: Enabling Durability and Sustainability
Flexible display technology, enabled by advancements in substrates and materials, offers a sustainable path forward:
- Durability: Flexible displays are less prone to cracking, reducing the need for replacements and associated e-waste.
- Lightweight Design: Lighter materials reduce shipping emissions and costs.
From foldable smartphones to rollable TVs, these displays cater to evolving consumer demands while addressing environmental concerns.
Smart Coatings and Self-Healing Materials
Innovative coatings and materials are being developed to extend the lifespan of LCDs and reduce maintenance:
- Anti-Reflective Coatings: These improve display efficiency by reducing energy loss through glare, making screens more energy-efficient.
- Self-Healing Polymers: Materials that can repair minor scratches and damage on their own enhance the longevity of displays, reducing waste from replacements.
Looking Ahead: The Potential of Emerging Technologies
The integration of these green technologies is not just a vision but a growing reality. Over the next decade, the industry can expect:
- Wider Adoption: Quantum dots, bio-based polymers, and advanced recycling systems are expected to become standard features in LCD manufacturing.
- Cost Reductions: As these technologies scale, their costs are predicted to decrease, making sustainable practices more accessible to smaller manufacturers.
- Innovation Synergies: Combining multiple technologies, such as quantum dots with graphene-based electrodes, could further amplify sustainability benefits.
By embracing these innovations, the LCD manufacturing industry can achieve significant strides toward sustainability, balancing performance, cost-effectiveness, and environmental responsibility.
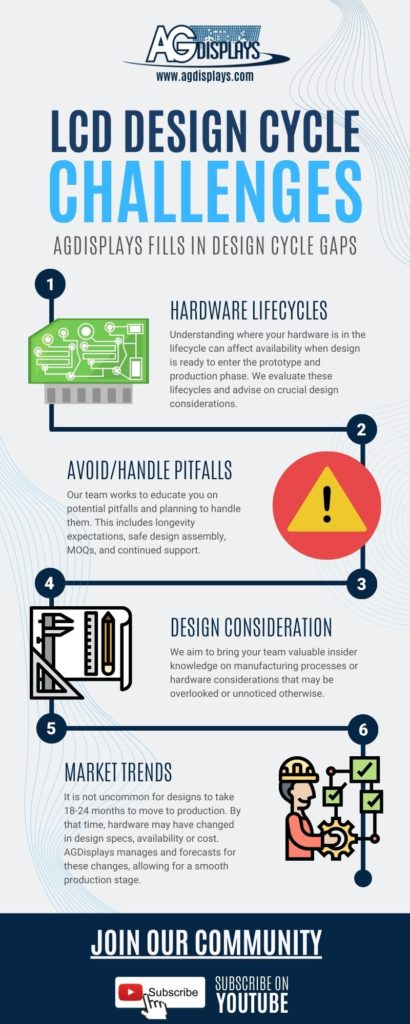
The Future Economics of Sustainable LCD Manufacturing
The transition to sustainable LCD manufacturing is not just an environmental necessity but an economic opportunity. While the upfront costs of adopting green technologies and practices can be significant, the long-term benefits—both financial and environmental—make a strong case for change. Over the next decade, sustainable manufacturing is expected to reshape the industry in several key ways.
Market Growth and Investment
The global market for sustainable electronics is projected to grow substantially. According to Allied Market Research, the green electronics market, which includes sustainable LCDs, was valued at approximately $41 billion in 2020 and is expected to reach $103 billion by 2030, growing at a compound annual growth rate (CAGR) of 9.1%. This growth is fueled by increasing consumer demand for eco-friendly products and stricter regulatory requirements for electronic manufacturing.
Cost Savings from Efficiency
Sustainable manufacturing processes often lead to cost savings in the long run:
- Energy-Efficient Technologies: Adopting low-energy production techniques can reduce electricity costs by up to 30%. For instance, LED-based photolithography not only consumes less energy but also reduces wear and tear on equipment, leading to lower maintenance costs.
- Water Recycling: Implementing closed-loop water recycling systems can save manufacturers millions of liters annually. With the cost of industrial water usage rising, this translates to significant financial savings.
- Material Recovery: Recycling LCD components like indium, glass, and polymers reduces the need for costly virgin materials. Advanced recycling processes have made material recovery more efficient, with recovery rates for indium now reaching 90% in some facilities.
Consumer Willingness to Pay
Studies suggest that consumers are increasingly willing to pay a premium for sustainable products:
- A Nielsen survey found that 73% of global consumers would adjust their purchasing habits to reduce environmental impact, and 41% are willing to pay more for products with proven sustainability.
- Eco-conscious branding and certifications like EPEAT and Energy Star can justify higher price points, creating new revenue streams for manufacturers.
Regulatory and Tax Incentives
Governments worldwide are introducing policies to encourage sustainable manufacturing:
- Tax Credits and Grants: Many countries offer tax breaks and grants to companies investing in renewable energy, water recycling, and green technologies.
- Carbon Pricing: As carbon taxes and cap-and-trade systems become more widespread, adopting energy-efficient and low-emission manufacturing processes can help companies avoid penalties and reduce costs.
Job Creation and Economic Activity
The transition to sustainable practices is also creating new economic opportunities:
- The global green technology and sustainability market is expected to grow at a CAGR of 22.5% from 2022 to 2030, according to Grand View Research. This growth will drive demand for skilled professionals in areas like recycling technology, green chemistry, and energy-efficient engineering.
- Investments in renewable energy and sustainable supply chains stimulate local economies, creating jobs in related sectors.
Potential Challenges
Despite these opportunities, the shift to sustainable LCD manufacturing also comes with economic hurdles:
- Upfront Costs: Transitioning to sustainable technologies requires significant capital investment. However, companies that adopt these changes early are likely to gain a competitive advantage as regulations tighten and consumer preferences shift.
- Market Dynamics: Balancing the cost of sustainability with the affordability of products remains a challenge, particularly in price-sensitive markets.
Long-Term Outlook
As sustainability becomes a non-negotiable aspect of doing business, the economics of LCD manufacturing will increasingly favor those who embrace greener practices. By 2030, sustainable manufacturing is expected to:
- Reduce overall production costs by 15-20% through efficiency gains and material recovery.
- Enhance brand value and market share for companies leading in sustainability.
- Contribute significantly to global efforts to combat climate change by reducing greenhouse gas emissions.
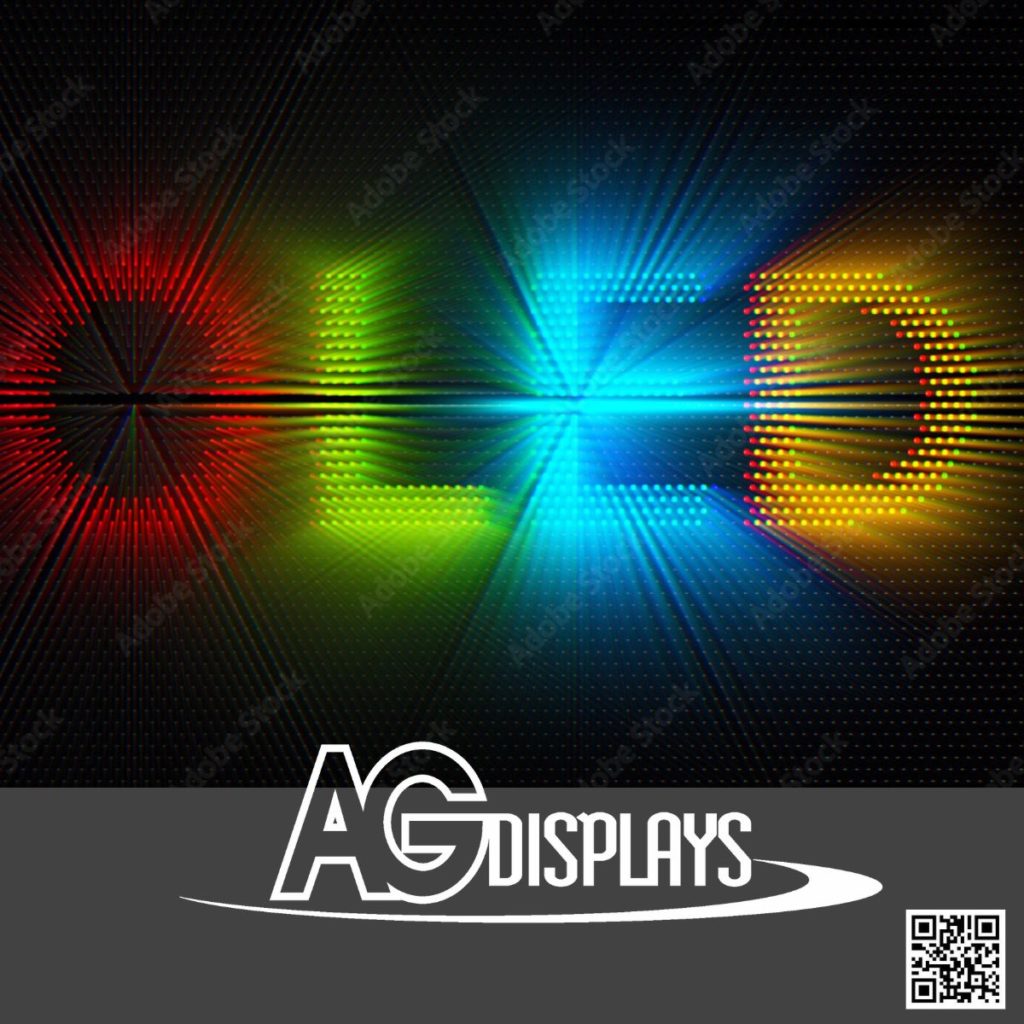
The Road Ahead: Challenges and Opportunities
While there has been significant progress in the field of sustainable LCD technology, the journey is far from complete. A number of challenges persist, and addressing them will be crucial for the industry’s future.
- Scaling Technologies: Innovative materials, such as graphene-based Transparent Conductive Materials (TCMs), promise to revolutionize the performance and efficiency of LCDs. However, these materials are still in the early stages of development. For wide-scale adoption, extensive research, testing, and investment are necessary to perfect these technologies and reduce production costs. Furthermore, scaling these innovations from laboratory settings to commercial manufacturing requires overcoming logistical hurdles, such as supply chain development and achieving economies of scale.
- Economic Barriers: The transition to sustainable LCD technologies often requires significant upfront investment. Small and medium-sized manufacturers, in particular, may find it difficult to bear the financial burden of adopting new processes, sourcing sustainable materials, or upgrading their existing infrastructure to meet green standards. Overcoming this challenge may require a more structured approach to financing, such as subsidies or loans from governments or partnerships with larger companies that can shoulder some of the initial costs.
- Global Recycling Infrastructure: The need for a robust global electronic waste recycling infrastructure is pressing. Many materials used in LCDs, including rare earth metals and certain chemicals, are finite and difficult to recover. Without the capacity to recycle electronic waste efficiently, these valuable materials cannot be reintroduced into production cycles, leading to resource depletion and environmental harm. Expanding the recycling network on a global scale would require investment in advanced recycling technologies and a coordinated effort between countries, industries, and private entities to ensure effective waste management and material recovery.
Opportunities for a Sustainable Future
Despite these challenges, the opportunities for a more sustainable future for LCD technology are vast. Collaboration between stakeholders can drive meaningful progress:
- Collaboration Between Stakeholders: The path forward will depend on a collective effort involving manufacturers, regulators, and consumers. Manufacturers can innovate and improve sustainability within their operations, while regulators can create policies that incentivize green technologies, waste management, and the responsible sourcing of materials. At the same time, consumers are becoming more environmentally conscious and demanding sustainable products, driving market demand. This trifecta of action can spark rapid changes across the industry.
- Innovation in Design for Disassembly: Designing LCDs for disassembly—where individual components can be easily separated and reused—could simplify recycling efforts and reduce the environmental impact of discarded devices. As more manufacturers adopt this philosophy, the entire lifecycle of LCD technology will become more circular, with less waste ending up in landfills.
- Emerging Green Manufacturing Techniques: As new production methods, such as 3D printing and bioplastics, continue to advance, manufacturers could explore new ways to reduce energy consumption, material waste, and emissions during the manufacturing process. These technologies could also open up opportunities to integrate more sustainable materials into LCD displays without compromising performance or cost.
- Consumer Education and Responsibility: Educating consumers about the environmental impact of their electronic purchases and encouraging recycling programs can create a more sustainable ecosystem. Consumers play a pivotal role in closing the loop of production and disposal, ensuring that devices are properly recycled and that valuable materials are returned to the supply chain.
AGDisplays: A Champion of Sustainability in LCD Enhancements
As a leader in LCD enhancement and repair solutions, AGDisplays is uniquely positioned to address the growing demand for sustainable practices in the display industry. The company combines its expertise in innovative display solutions with a commitment to environmental responsibility, focusing on extending the lifecycle of LCD products and reducing waste.
Lifecycle Extension through LCD Enhancements
AGDisplays provides value-added services that improve the durability, efficiency, and usability of LCDs. By enhancing existing displays, the company helps its clients maximize the utility of their products, thereby reducing the need for replacements and minimizing e-waste. Key services include:
- Optical Bonding: This process strengthens displays, reduces glare, and improves readability in harsh environments, extending product lifespan and preventing premature disposal.
- Backlight Upgrades: Upgrading traditional backlighting systems to energy-efficient LED solutions reduces power consumption while maintaining or enhancing display performance.
- Protective Solutions: Anti-glare coatings, ruggedized glass, and protective laminations ensure that displays withstand wear and tear, minimizing the frequency of replacements.
Sustainable Repair and Refurbishment
AGDisplays’ repair and refurbishment services provide an eco-friendly alternative to discarding damaged displays. By restoring functionality and upgrading existing units, the company plays a direct role in reducing waste and supporting a circular economy:
- Recycling-Compatible Practices: Refurbished displays are often integrated with recyclable components, ensuring sustainability even at the end of their extended lifecycle.
- Cost and Resource Savings: Clients benefit from reduced costs while also contributing to sustainability goals by reusing refurbished displays rather than purchasing new ones.
Custom Solutions for Greener Operations
AGDisplays works closely with clients to deliver custom solutions tailored to their sustainability goals. By leveraging its deep understanding of LCD technology, the company offers designs and enhancements that:
- Incorporate Eco-Friendly Materials: Whenever possible, AGDisplays integrates components made from recycled or bio-based materials into its solutions.
- Optimize Energy Efficiency: Custom displays designed with low-power requirements help businesses reduce their overall energy footprint.
- Support Recycling Initiatives: AGDisplays ensures that its products and enhancements align with industry best practices for recycling and material recovery.
Collaboration with Industry Partners
As a forward-thinking organization, AGDisplays actively collaborates with manufacturers and suppliers who prioritize sustainability. This ensures that the materials and components used in its enhancements adhere to environmentally responsible standards.
Education and Advocacy
AGDisplays is committed to raising awareness about the importance of sustainable practices within the display industry. The company regularly provides clients with information on the environmental benefits of choosing repair, refurbishment, and enhancement services over new purchases.
Real-World Impact
By focusing on lifecycle extension, repair, and custom enhancements, AGDisplays contributes to a significant reduction in e-waste. For example:
- Backlight Retrofits: A recent AGDisplays project involved upgrading the backlights of industrial monitors to LED systems, reducing energy consumption by 25% and extending product lifespan by several years.
- Optical Bonding Solutions: AGDisplays partnered with a medical equipment manufacturer to ruggedize its displays, preventing damage and reducing annual replacements by 40%.
With these initiatives, AGDisplays is a critical player in making the LCD industry more sustainable, offering practical solutions that benefit both the environment and its clients.
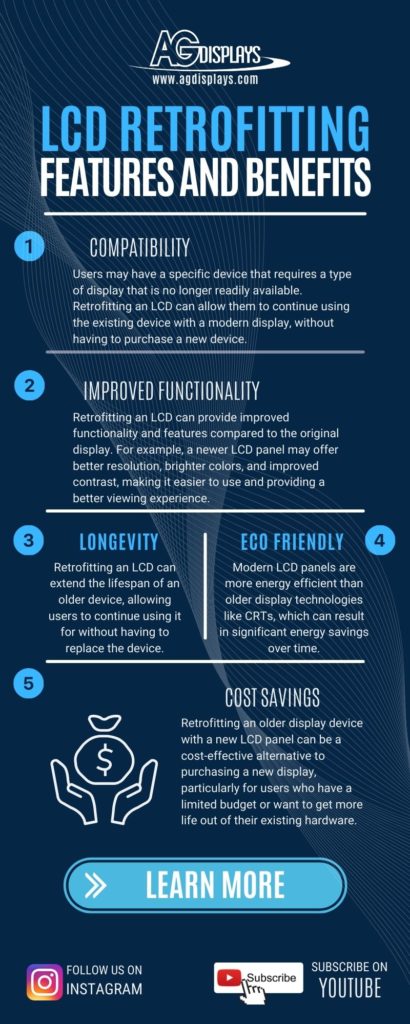
Conclusion
Sustainability in LCD manufacturing is not just an ethical imperative—it’s a business necessity. Innovations in quantum dots, transparent conductive materials, recyclable components, and water recycling are transforming the industry. Companies like AGDisplays, LG Display, and Samsung Display are leading the way by embracing sustainable practices, focusing on lifecycle extension, and investing in green technologies.
Through its repair, refurbishment, and enhancement services, AGDisplays exemplifies how businesses can contribute to a greener future for LCD technology. By leveraging innovative solutions and fostering collaboration across the supply chain, the company not only reduces its environmental footprint but also empowers its clients to do the same.
The future of LCDs is green. By continuing to innovate and adopt sustainable practices, manufacturers and service providers can ensure that the displays we rely on every day contribute to a healthier, more sustainable planet.
To browse a selection of AGDisplays cutting edge display products, visit our Shopify store: https://shop.agdisplays.com/