In the fast-evolving world of aerospace, displays are far more than mere screens—they are mission-critical instruments that must perform with unwavering precision in some of the most unforgiving environments imaginable. From the cockpit of a commercial airliner soaring at 35,000 feet to the control panels of spacecraft pushing the boundaries of human exploration, aerospace displays face a unique set of challenges that test their durability, readability, and reliability. These challenges stem from extreme temperatures, low atmospheric pressure, intense ultraviolet (UV) radiation, constant vibration, and electromagnetic interference (EMI). At AGDisplays, we specialize in engineering display solutions that rise to these challenges, ensuring safety, performance, and mission success. This article delves into the complexities of high-altitude environments, the engineering innovations that address them, and the cutting-edge advancements shaping the future of aerospace display technology.
The High-Altitude Environment: A Test of Endurance
High-altitude environments—whether in the stratosphere or beyond Earth’s atmosphere—subject displays to conditions that ordinary consumer-grade electronics simply cannot withstand. Understanding these conditions is the first step in designing displays that can endure the rigors of aerospace applications.
Extreme Temperatures
At cruising altitudes, external temperatures can plummet to -40°C or lower, while internal cockpit or spacecraft environments may fluctuate dramatically. These extremes can impair the performance of liquid crystal displays (LCDs), cause electronic components to malfunction, or lead to thermal stress in materials. For instance, liquid crystals in traditional LCDs may freeze or respond sluggishly in subzero conditions, compromising readability.
Low Atmospheric Pressure
At high altitudes, atmospheric pressure drops significantly, creating challenges such as outgassing, where trapped gases in display materials escape and potentially damage components. Low pressure can also exert mechanical stress on display assemblies, risking structural failure if not properly addressed.
Intense UV Radiation
Thinner atmospheric layers at high altitudes offer less protection from UV radiation, which can degrade display materials over time. Prolonged exposure may cause discoloration, reduced optical clarity, or weakened structural integrity in plastics and coatings.
Vibration and Shock
Aircraft and spacecraft endure constant vibration from engines, turbulence, or launch sequences, as well as occasional shocks from maneuvers or landings. These forces can dislodge components, crack screens, or disrupt electrical connections if displays are not engineered for resilience.
Electromagnetic Interference (EMI)
High-altitude environments amplify the risk of EMI, as electronic systems operate in close proximity and cosmic radiation becomes more prevalent in space. EMI can interfere with display functionality, causing flickering, data corruption, or complete system failure.

Engineering Solutions: Building Displays That Thrive
To overcome these challenges, aerospace displays require a multidisciplinary approach that integrates advanced materials, innovative engineering, and rigorous testing. AGDisplays leverages decades of expertise to deliver tailored solutions that meet the stringent demands of aerospace applications. Below, we explore the key engineering strategies employed to ensure high-altitude performance.
1. Thermal Management
Maintaining optimal performance in extreme temperatures is paramount for aerospace displays. Engineers employ several techniques to address thermal challenges:
- Wide Operating Temperature Ranges: Industrial-grade LCDs are designed to function reliably between -40°C and 85°C, ensuring consistent performance in both frigid high-altitude conditions and heat-intensive cockpit environments.
- Integrated Heaters and Cooling Systems: Displays often incorporate heaters to maintain stable internal temperatures during cold starts, while cooling systems, such as heat sinks or fans, dissipate excess heat in warmer conditions. These systems prevent thermal stress and ensure that components operate within their optimal temperature range.
- Thermally Stable Materials: The use of materials with low thermal expansion coefficients minimizes warping or cracking due to temperature fluctuations.
2. Pressure Resistance
Low-pressure environments demand displays that can maintain structural integrity and prevent internal damage:
- Airtight Enclosures: Sealed display designs prevent outgassing by containing gases within the assembly. These enclosures are often constructed with robust gaskets and seals to maintain a stable internal environment.
- Pressure-Resistant Materials: Engineers select materials, such as high-strength glass or specialized polymers, that can withstand mechanical stress caused by pressure differentials without compromising optical performance.
- Vacuum Bonding: Optical bonding techniques, which eliminate air gaps between display layers, enhance structural integrity and reduce the risk of damage in low-pressure environments.
3. UV Protection
To combat the effects of intense UV radiation, displays are engineered with protective measures:
- UV-Resistant Coatings: Specialized coatings are applied to display surfaces to block or absorb UV radiation, preventing degradation of underlying materials.
- UV-Stable Materials: Components such as polarizers, adhesives, and substrates are chosen for their ability to resist UV-induced discoloration or embrittlement, ensuring long-term optical clarity and durability.
- Anti-Reflective (AR) Films: In addition to UV protection, AR films enhance visibility by reducing glare, which is particularly critical in brightly lit cockpits or space environments.
4. Vibration and Shock Mitigation
Displays must be built to withstand constant movement and sudden impacts:
- Reinforced Frames: Heavy-duty frames, often made from aluminum or composite materials, provide structural integrity and protect internal components from vibration-induced fatigue.
- Shock-Absorbing Mounts: Elastomeric mounts or dampening systems absorb and dissipate vibrational energy, safeguarding delicate electronics and preventing misalignment.
- Ruggedized Components: Internal components, such as connectors and circuit boards, are secured with locking mechanisms or conformal coatings to prevent loosening during operation.
5. EMI Shielding
Protecting displays from electromagnetic interference is critical in high-altitude environments:
- Conductive Coatings and Filters: Transparent conductive coatings, such as indium tin oxide (ITO), are applied to display surfaces to shield against EMI without compromising optical clarity.
- Shielded Cabling: High-quality shielded cables minimize EMI transmission to and from the display, ensuring reliable data transfer.
- Grounding Systems: Robust grounding designs reduce the risk of EMI-induced disruptions by directing stray currents away from sensitive components.
Case Study: Customizing LCDs for Aerospace Excellence
To illustrate the practical application of these engineering principles, consider a project undertaken by AGDisplays to modify consumer-grade LCD panels for aerospace use. The client required displays for a commercial aircraft cockpit, with stringent requirements for brightness, color consistency, readability in brightly lit environments, and compliance with Federal Aviation Administration (FAA) standards, including DO-160 specifications for environmental conditions and EMI.
Challenges
- Brightness and Color Uniformity: Consumer-grade LCDs often exhibit variations in brightness and color temperature, which are unacceptable in aerospace applications where readability is critical.
- Environmental Durability: The displays needed to withstand temperature extremes, vibration, and low-pressure conditions without compromising performance.
- Regulatory Compliance: Meeting FAA and DO-160 standards required meticulous attention to EMI, optical performance, and structural integrity.
Solutions
- LED Backlighting: AGDisplays replaced fluorescent tubes with high-efficiency LED backlights, which offer superior brightness control, energy efficiency, and the ability to operate in extreme temperatures. This upgrade ensured consistent illumination across the display.
- Optical Calibration: Advanced calibration techniques were used to achieve uniform color temperature and brightness, eliminating variations and ensuring readability in diverse lighting conditions.
- Protective Glass Shields: The displays were fitted with optically bonded glass shields coated with anti-glare and UV-resistant films. This enhanced durability, reduced reflections, and protected against environmental stressors.
- EMI Reduction Measures: Conductive coatings and shielded cabling were implemented to meet DO-160 EMI specifications, ensuring reliable performance in the presence of electromagnetic noise.
Outcome
The customized displays exceeded client expectations, delivering exceptional readability, durability, and compliance with aerospace standards. The project demonstrated AGDisplays’ ability to transform off-the-shelf components into mission-critical solutions through innovative engineering and rigorous testing.
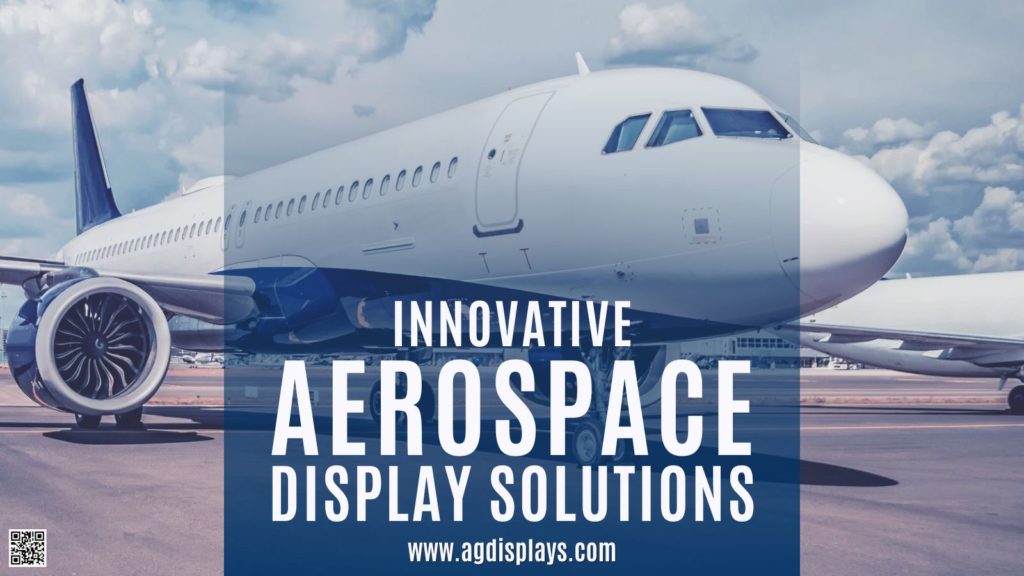
Advancements in Aerospace Display Technology
The aerospace industry is constantly pushing the boundaries of what’s possible, and display technology is evolving to keep pace. AGDisplays is at the forefront of these advancements, integrating cutting-edge innovations to enhance performance in high-altitude environments.
Radiation-Hardened Components
For spacecraft operating beyond Earth’s atmosphere, cosmic radiation poses a significant threat to electronic components. Radiation-hardened displays use specialized materials and circuit designs to resist damage from high-energy particles, ensuring reliable operation during long-duration missions.
Sunlight-Readable Displays
High-brightness backlights, often exceeding 1000 nits, combined with anti-reflective coatings, make sunlight-readable displays a game-changer for aerospace applications. These displays remain legible in direct sunlight, ensuring pilots and astronauts can access critical information without interruption.
Night Vision Compatibility
Displays designed for night vision compatibility (NVIS) are engineered to emit minimal infrared light, preventing interference with night vision goggles. This is achieved through specialized filters and backlighting that maintain readability in low-light conditions without compromising NVIS performance.
Touchscreen Interfaces
Modern aerospace displays increasingly incorporate touchscreen functionality, allowing for intuitive interaction in complex systems. These touchscreens are engineered to respond accurately even when operators wear gloves, using technologies such as projected capacitive (PCAP) touch or infrared touch sensors.
Flexible and Curved Displays
Emerging flexible and curved display technologies offer new possibilities for aerospace applications. These displays can conform to non-planar surfaces, such as curved cockpit dashboards, improving ergonomics and maximizing space efficiency.
Augmented Reality (AR) Integration
AR-enabled displays are gaining traction in aerospace, overlaying critical data—such as navigation cues or system diagnostics—directly onto the pilot’s or astronaut’s field of view. These systems require high-resolution displays with low latency and precise optical alignment.
Energy Efficiency
As aerospace systems strive for greater sustainability, energy-efficient displays are becoming a priority. Advances in LED backlighting, low-power electronics, and adaptive brightness control reduce power consumption without sacrificing performance.
The Role of Testing and Validation
Ensuring that aerospace displays can withstand high-altitude conditions requires rigorous testing and validation. AGDisplays employs a comprehensive testing regimen to verify performance under simulated environmental stressors:
- Thermal Cycling: Displays are subjected to rapid temperature changes to assess their resilience to thermal shock.
- Vibration and Shock Testing: Simulated flight conditions, including turbulence and launch vibrations, confirm structural integrity.
- Pressure Testing: Low-pressure chambers replicate high-altitude environments to evaluate outgassing and material performance.
- EMI Testing: Displays are tested in electromagnetic environments to ensure compliance with standards like DO-160.
- UV Exposure Testing: Prolonged exposure to UV radiation verifies the effectiveness of protective coatings and materials.
These tests, combined with adherence to industry standards such as MIL-STD-810 and DO-160, ensure that AGDisplays’ solutions meet the highest benchmarks for reliability and performance.
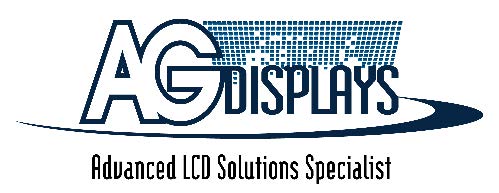
The Future of Aerospace Displays
As aerospace missions grow more ambitious—encompassing commercial space travel, deep-space exploration, and autonomous aircraft—the demands on display technology will only intensify. Emerging trends point to several exciting developments:
- Micro-LED Technology: Offering superior brightness, contrast, and energy efficiency, micro-LED displays are poised to replace traditional LCDs in aerospace applications.
- Artificial Intelligence (AI) Integration: AI-driven displays could dynamically adjust brightness, contrast, or content based on environmental conditions or operator needs, enhancing usability and safety.
- Holographic Displays: Holographic interfaces could revolutionize cockpit design, providing 3D visualizations of flight data or terrain without the need for physical screens.
- Biometric Integration: Displays with integrated biometric sensors could monitor pilot or astronaut health, providing real-time feedback on stress levels or fatigue.
At AGDisplays, we are committed to staying ahead of these trends, partnering with aerospace manufacturers to develop next-generation display solutions that empower safer, more efficient missions.
Conclusion
Designing displays for high-altitude aerospace applications is a complex endeavor that requires expertise in materials science, optical engineering, and environmental testing. By addressing challenges such as extreme temperatures, low pressure, UV radiation, vibration, and EMI, AGDisplays delivers solutions that combine reliability, readability, and innovation. From customized LCDs to cutting-edge advancements like radiation-hardened components and AR integration, our displays are engineered to perform where failure is not an option.
As the aerospace industry ventures further into uncharted territory, AGDisplays remains a trusted partner, providing display technology that meets the demands of today and anticipates the challenges of tomorrow. Whether in the cockpit of a commercial jet or the command module of a spacecraft, our displays are built to inspire confidence and ensure mission success.