The industrial LCD display industry plays a pivotal role in modern technology, providing visual interfaces that are essential in a wide range of applications. These displays are designed to meet the rigorous demands of industrial environments, offering high durability, reliability, and often specialized features tailored to specific sectors.
The industrial LCD display market has witnessed significant growth over the years, driven by advancements in technology, increased automation, and the growing need for efficient and accurate data visualization in various industries. These displays come in different sizes, resolutions, and form factors, catering to diverse requirements across sectors such as manufacturing, healthcare, transportation, energy, and more.
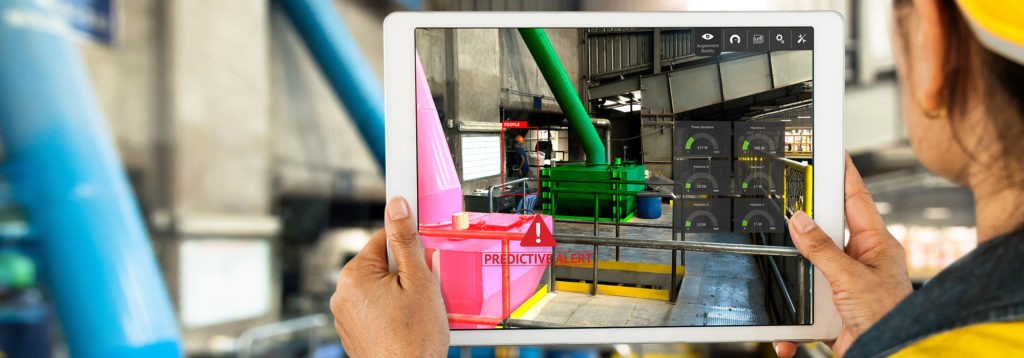
I. The Importance of Industrial LCD Displays in Various Sectors
- Manufacturing and Automation: Industrial LCD displays are integral to modern manufacturing processes, providing real-time monitoring and control interfaces for automated systems. These displays enhance efficiency, reduce human error, and contribute to seamless production workflows.
- Healthcare: In the healthcare sector, industrial LCD displays are utilized in medical imaging, patient monitoring, and diagnostic equipment. The high resolution and color accuracy of these displays are crucial for accurate interpretation of medical images and data, supporting healthcare professionals in delivering optimal patient care.
- Transportation: From aviation to automotive industries, industrial LCD displays are essential for navigation systems, in-flight entertainment, control panels, and vehicle dashboards. These displays contribute to safety, efficiency, and overall operational effectiveness in transportation sectors.
- Energy and Utilities: In the energy sector, industrial LCD displays play a crucial role in monitoring and controlling power plants, distribution systems, and renewable energy installations. These displays enable operators to visualize critical data, identify issues, and respond promptly to ensure the reliability and efficiency of energy production.
- Logistics and Warehousing: Industrial LCD displays are used in logistics and warehousing for inventory management, order picking, and tracking. These displays facilitate smooth operations, reduce errors in the supply chain, and enhance overall productivity.
- Military and Defense: In military applications, industrial LCD displays are employed in command and control centers, surveillance systems, and military vehicles. The rugged design of these displays ensures they can withstand harsh conditions, providing reliable performance in mission-critical scenarios.
- Environmental Monitoring: Industrial LCD displays are utilized in environmental monitoring systems, helping professionals visualize and analyze data related to air quality, weather conditions, and environmental parameters. This is crucial for decision-making in environmental research and management.
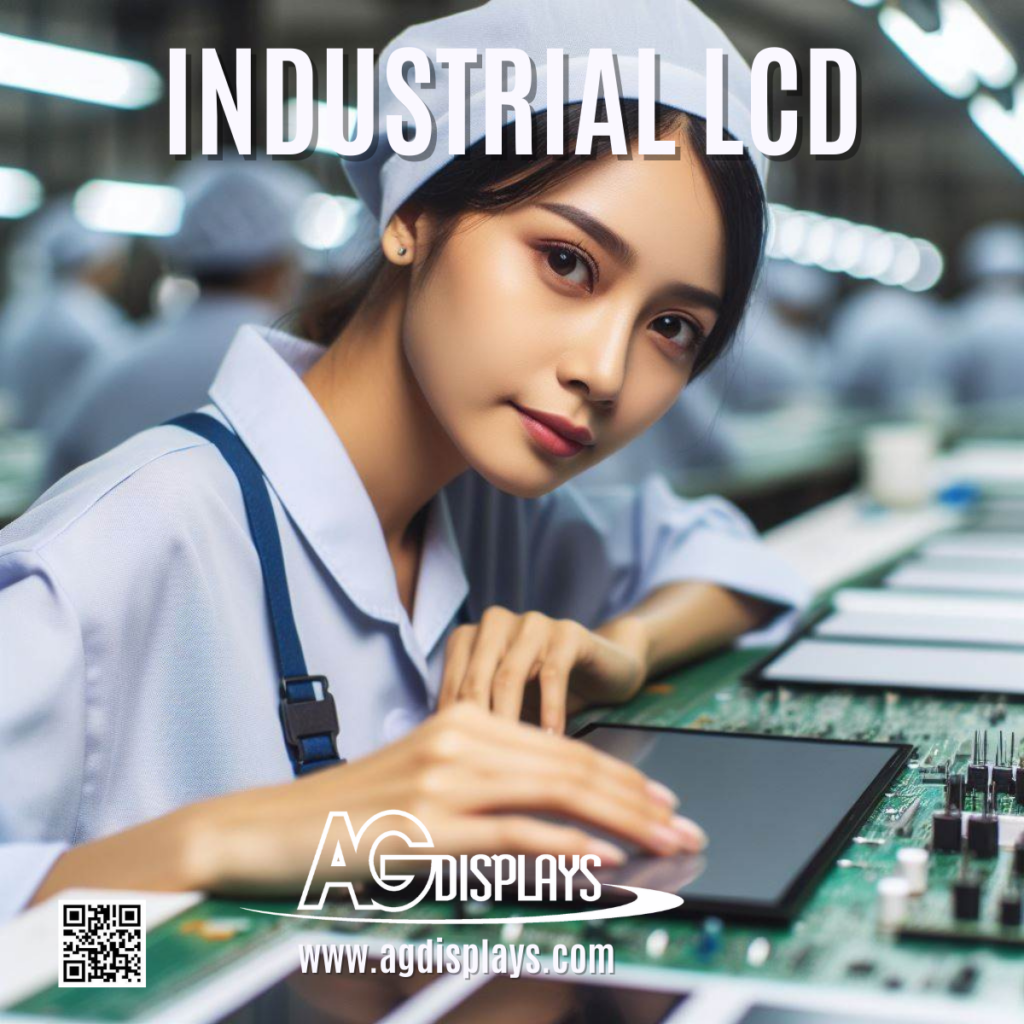
II. Manufacturing Process
A. Raw Materials and Components
- Key Materials Used in LCD Display Production: The production of LCD displays involves several crucial materials. The most fundamental component is the liquid crystal display (LCD) itself, composed of liquid crystal material sandwiched between two layers of glass or other substrates. The glass substrates are typically made from high-quality materials like amorphous silicon, while the liquid crystals may be nematic, smectic, or other types, depending on the desired characteristics of the display. Other essential materials include color filters, polarizers, backlight units (LEDs or other light sources), and conductive materials such as indium tin oxide (ITO) for transparent electrodes.
- Manufacturing Processes for LCD Panels: The production of LCD panels is a highly intricate process. It typically involves several stages, including glass substrate preparation, deposition of thin-film transistors (TFTs) for active matrix displays, application of color filters, alignment of liquid crystals, and final assembly. Photolithography and chemical processes are often used to pattern the layers precisely. The manufacturing process also includes steps like cell gap control, rubbing, and sealing, all of which contribute to the quality and performance of the LCD panel. Each step requires precision and adherence to strict quality standards to ensure the final product meets the required specifications.
B. Assembly and Testing
- Overview of the Assembly Line: The assembly of LCD displays involves the integration of various components into a finished product. The assembly line typically consists of stations where different parts are added, and specific processes are carried out. This includes attaching the backlight unit, connecting control electronics, sealing the LCD panel, and encapsulating the entire assembly. Automated machinery is often employed for tasks like precision placement of components and soldering. The assembly line is designed for efficiency, with each station contributing to the gradual transformation of individual components into a fully functional LCD display.
- Quality Control and Testing Procedures: Quality control is a critical aspect of the LCD display manufacturing process to ensure that the final products meet stringent performance standards. Various testing procedures are implemented at different stages of assembly. This includes testing individual components for defects before assembly, inspecting the alignment and integrity of the LCD panel during the manufacturing process, and conducting thorough quality checks on the finished product. Testing may involve assessing color accuracy, brightness, contrast ratio, pixel integrity, and overall functionality. Automated testing equipment is often used for efficiency and accuracy, helping identify and rectify any defects or inconsistencies in the displays before they reach the final stages of production.
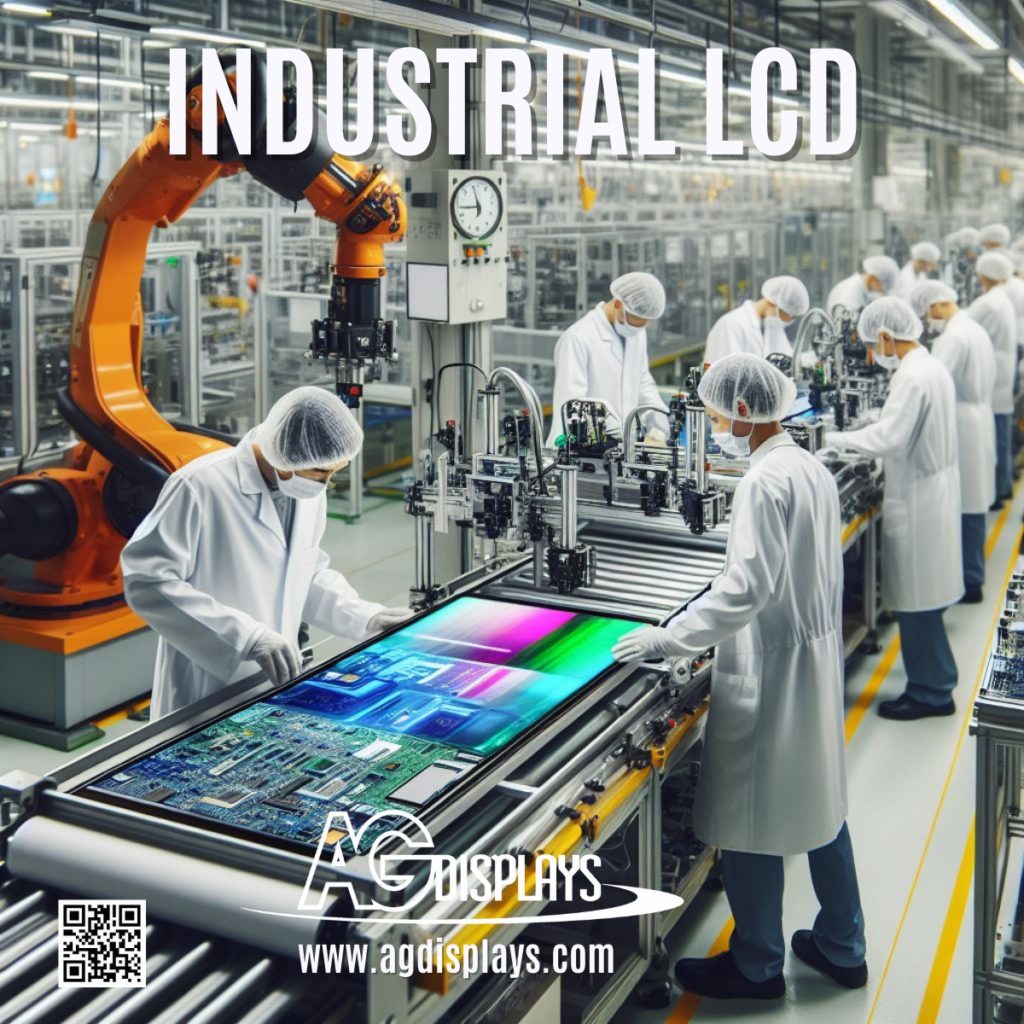
III. Factory Operations
A. Factory Environments and Facilities
- Cleanroom Requirements: The production of LCD displays demands extremely controlled environments to prevent dust, contaminants, and other particles from affecting the quality of the displays. Cleanrooms are essential in LCD manufacturing facilities to maintain a sterile atmosphere. These cleanrooms adhere to stringent cleanliness standards, often classified by their level of air cleanliness. The air is filtered and regulated to minimize the presence of microscopic particles. Workers within these cleanrooms typically wear specialized clothing such as cleanroom suits, gloves, and shoe covers to further reduce the risk of contamination.
- Advanced Technologies Used in LCD Production: LCD production involves the utilization of cutting-edge technologies to achieve precision and efficiency. Photolithography, a process used for patterning thin films on substrates, plays a crucial role. Advanced machinery for deposition, etching, and bonding processes are employed to create intricate patterns and ensure the uniformity of layers. Automated robotic systems are often used for handling and assembling delicate components, contributing to both speed and precision in the manufacturing process. Furthermore, the implementation of advanced technologies like quantum dots for enhanced color reproduction and organic light-emitting diodes (OLEDs) in certain types of displays represents ongoing innovations in the field.
B. Workforce and Skill Requirements
- Overview of the Skilled Labor Force: The workforce involved in LCD manufacturing comprises skilled individuals with expertise in various disciplines. Engineers and technicians specializing in electronics, materials science, and optics are essential for designing and maintaining the sophisticated machinery used in the production process. Additionally, assembly line workers with a meticulous eye for detail are crucial for the precise assembly of components. Quality control personnel play a vital role in ensuring that the final products meet the required standards. In cleanroom environments, specialized training is necessary to work within the controlled conditions.
- Training Programs for Factory Workers: Given the specialized nature of LCD manufacturing, comprehensive training programs are essential for factory workers. Training may cover a range of topics, including understanding the intricacies of the production process, operating and maintaining specialized machinery, adhering to cleanroom protocols, and implementing quality control measures. Ongoing training is often provided to keep workers updated on the latest technologies and industry best practices. Many manufacturing facilities collaborate with educational institutions or provide in-house training to ensure that their workforce possesses the necessary skills and knowledge to contribute effectively to the production process.
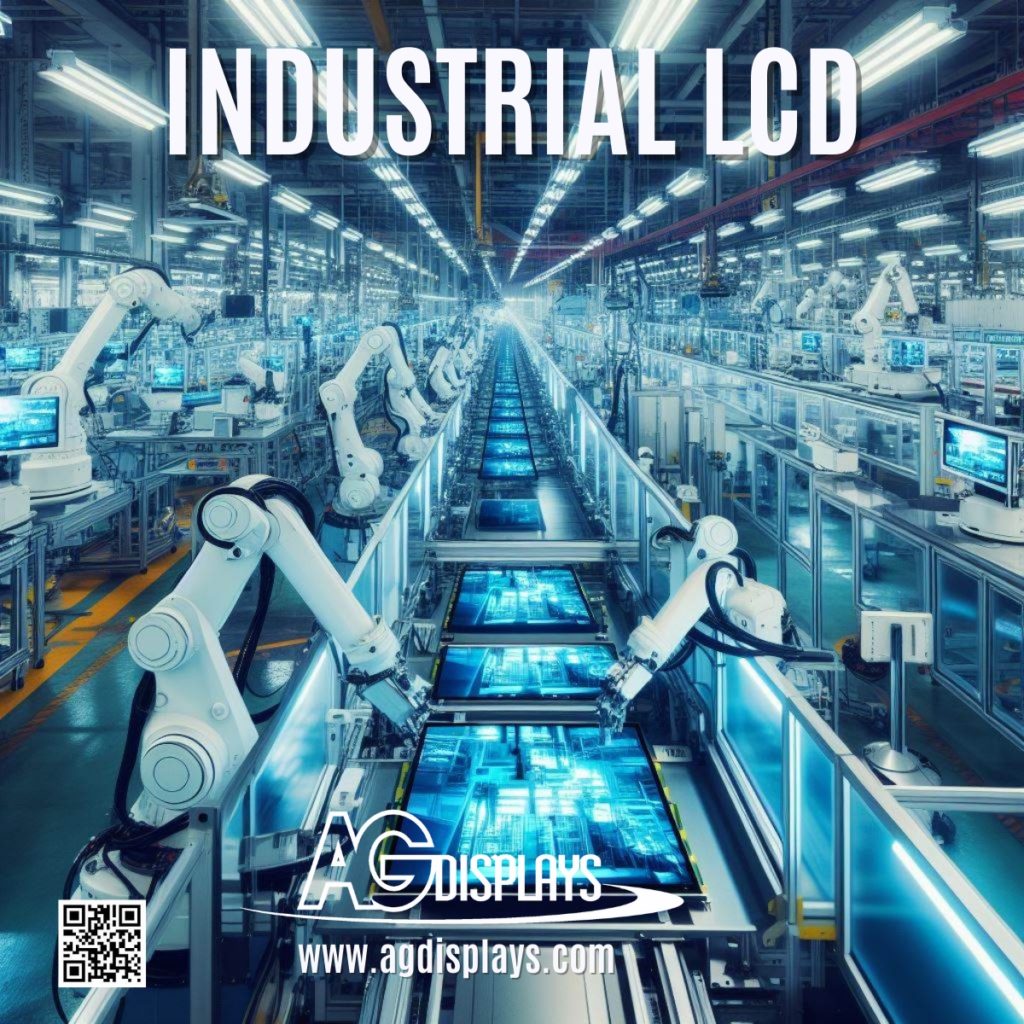
IV. Technological Innovations
A. Emerging Technologies in LCD Display Manufacturing
- OLED vs. LCD Displays: OLED (Organic Light-Emitting Diode) displays represent a significant advancement in display technology compared to traditional LCD (Liquid Crystal Display) technology. OLED displays offer improved contrast ratios, faster response times, and greater flexibility in design due to their ability to emit light directly from organic compounds. The absence of a backlight in OLED displays allows for thinner and more flexible screens, contributing to the development of innovative form factors such as curved and foldable displays. While OLED displays have gained popularity in premium smartphones and high-end TVs, ongoing research and development continue to explore ways to enhance their efficiency, lifespan, and affordability for broader application in various industries.
- Advances in Touchscreen Technology: Touchscreen technology has seen continuous evolution, enhancing the user interface in LCD displays. Capacitive touchscreens, which respond to the electrical properties of the human body, have become standard in modern devices. Innovations include multi-touch capabilities, enabling more complex and intuitive gestures. Furthermore, the integration of haptic feedback technologies provides users with tactile sensations, enhancing the overall user experience. Emerging technologies like in-display fingerprint sensors and gesture recognition systems are also making strides, expanding the possibilities for interactive displays in various applications, from consumer electronics to industrial control panels.
B. Industry 4.0 Integration
- Automation and Robotics in the Manufacturing Process: The integration of automation and robotics has become a cornerstone of Industry 4.0 in LCD display manufacturing. Automated robotic systems are employed for tasks such as precise handling of delicate components, assembly line processes, and quality control inspections. These robotic systems contribute to increased efficiency, reduced labor costs, and improved accuracy in manufacturing. Collaborative robots, or cobots, work alongside human operators, enhancing overall productivity while maintaining flexibility in production. The implementation of smart manufacturing systems ensures real-time monitoring and control of the production line, optimizing the entire manufacturing process.
- Data Analytics for Improved Efficiency: The use of data analytics has transformed the manufacturing landscape, offering insights into production processes, quality control, and overall efficiency. In LCD display manufacturing, data analytics are employed to monitor equipment performance, predict maintenance needs, and optimize production schedules. By analyzing vast amounts of data generated during the manufacturing process, manufacturers can identify patterns, detect anomalies, and make informed decisions to enhance efficiency and reduce downtime. Additionally, data analytics contribute to quality improvement by identifying and addressing potential issues before they impact the final product, leading to higher overall product reliability.
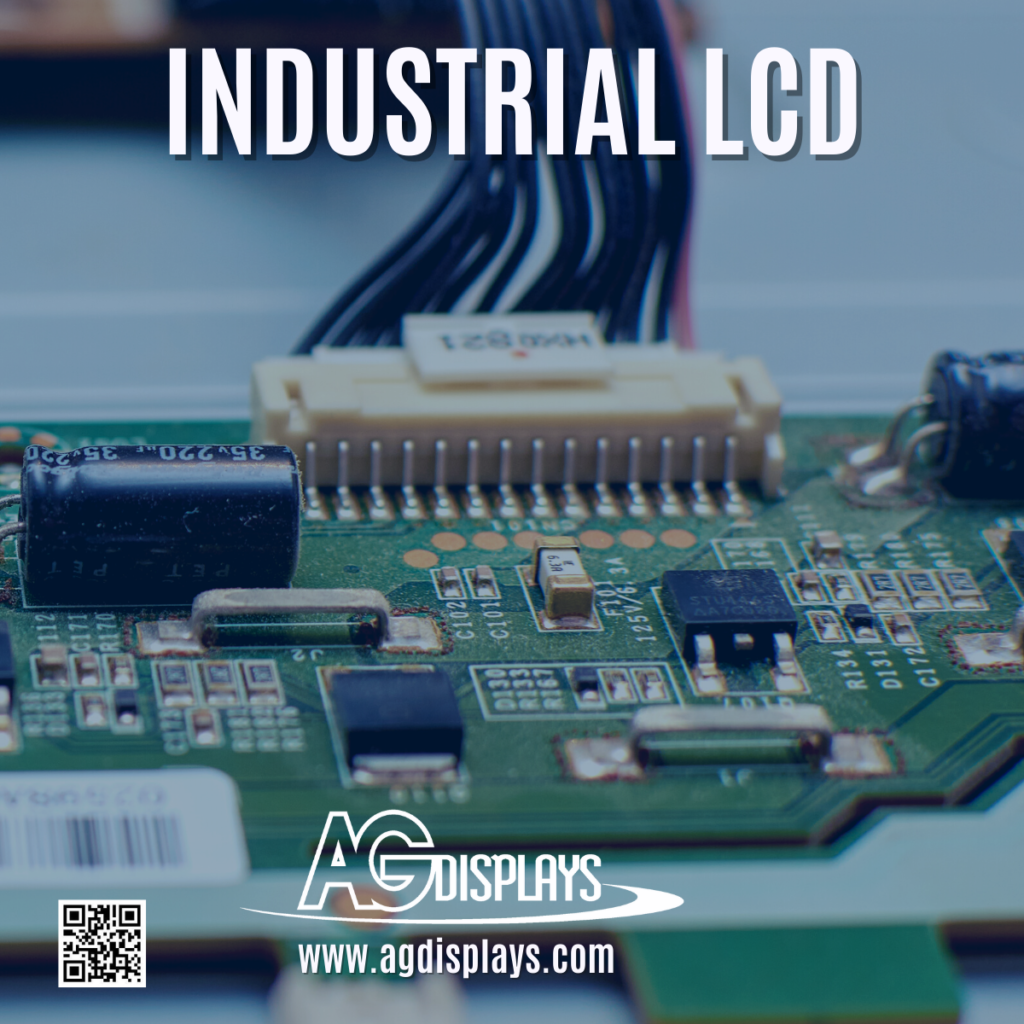
V. Supply Chain Management
A. Key Players in the Supply Chain
- Manufacturers of LCD Panels: At the core of the supply chain for LCD displays are the manufacturers of LCD panels. Companies such as Samsung Display, LG Display, AU Optronics, and BOE Technology are among the key players in producing high-quality LCD panels. These manufacturers invest heavily in research and development to improve panel technologies, increase production efficiency, and meet the diverse demands of various industries. They play a critical role in determining the performance, resolution, and features of the final LCD displays that are used in various applications.
- Suppliers of Raw Materials: The supply chain for LCD displays relies on a network of suppliers providing essential raw materials. These suppliers include manufacturers of glass substrates, chemicals for the production of liquid crystals, color filters, backlight units, and other critical components. Companies such as Corning, a major supplier of high-quality glass for display applications, and other specialty chemical providers contribute to the production of materials crucial for the manufacturing of LCD displays. The relationships between panel manufacturers and these suppliers are vital for ensuring a stable and high-quality supply of raw materials.
B. Logistics and Transportation
- Global Distribution Networks: The distribution of LCD displays involves complex global networks to meet the demands of diverse industries. Finished LCD panels are transported from manufacturing facilities to assembly plants or directly to original equipment manufacturers (OEMs) for integration into final products. Companies in the supply chain leverage global logistics networks to transport components and finished displays efficiently. International shipping, air freight, and land transportation are integral parts of these networks, ensuring timely delivery to meet market demands.
- Challenges in the Supply Chain: The supply chain for LCD displays faces various challenges, including geopolitical factors, trade regulations, and transportation constraints. Tariffs and trade disputes can impact the cost and availability of raw materials, affecting the overall cost structure of LCD displays. Additionally, disruptions in transportation due to natural disasters, geopolitical events, or global health crises can lead to delays in production and distribution. The industry is continually addressing these challenges through diversification of suppliers, strategic location planning for manufacturing facilities, and the implementation of contingency plans to mitigate risks.
Furthermore, the rapid evolution of technology in the display industry poses challenges related to the management of obsolete or outdated inventory. As new display technologies emerge, companies must navigate transitions smoothly, ensuring a balance between the supply of existing products and the integration of new technologies into their production processes.
VI. Market Trends and Consumer Demand
A. Market Analysis of Industrial LCD Displays
- Growth Projections and Market Segments: The market for industrial LCD displays is anticipated to experience significant growth, driven by technological advancements, increased automation across industries, and the growing demand for high-performance visual interfaces. Projections indicate sustained expansion, with an emphasis on key segments such as automotive, healthcare, manufacturing, and others.
- Automotive: The automotive sector continues to be a major contributor to the industrial LCD display market. Growing integration of advanced driver-assistance systems (ADAS), infotainment systems, and digital instrument clusters in vehicles fuels the demand for high-resolution and durable LCD displays. The market is expected to witness innovations such as augmented reality (AR) displays in windshields and advanced head-up displays (HUDs).
- Healthcare: In the healthcare industry, the demand for industrial LCD displays is driven by medical imaging equipment, patient monitoring systems, and diagnostic displays. The need for accurate visualization in surgeries and medical procedures underscores the importance of high-quality LCD panels. As medical technologies advance, the market is likely to see a surge in demand for displays with higher resolutions, improved color accuracy, and enhanced diagnostic capabilities.
- Manufacturing: The manufacturing sector benefits from the integration of LCD displays in control panels, Human-Machine Interface (HMI) systems, and automation equipment. As smart factories and Industry 4.0 initiatives gain momentum, there is a growing need for rugged and reliable displays that can withstand harsh industrial environments. The market is expected to see an increased demand for touchscreens and displays with advanced features to enhance operator efficiency and decision-making.
- Automotive: The automotive sector continues to be a major contributor to the industrial LCD display market. Growing integration of advanced driver-assistance systems (ADAS), infotainment systems, and digital instrument clusters in vehicles fuels the demand for high-resolution and durable LCD displays. The market is expected to witness innovations such as augmented reality (AR) displays in windshields and advanced head-up displays (HUDs).
- Factors Influencing Consumer Demand: Several factors influence consumer demand in the industrial LCD display market:
- Technological Advancements: Consumers seek displays with the latest technological features, including higher resolutions, faster response times, and improved color accuracy. Emerging technologies such as OLED displays, curved screens, and touch-sensitive interfaces contribute to consumer preferences.
- Durability and Reliability: Industries with demanding environments, such as manufacturing and automotive, prioritize displays that are durable and reliable. The ability of LCD displays to operate in challenging conditions, including exposure to extreme temperatures, vibrations, and dust, is a key factor influencing purchasing decisions.
- Customization and Flexibility: Consumers often require displays that can be customized to meet specific application requirements. The ability to tailor screen sizes, resolutions, and form factors to suit diverse industrial applications is a significant factor in consumer decision-making.
- Technological Advancements: Consumers seek displays with the latest technological features, including higher resolutions, faster response times, and improved color accuracy. Emerging technologies such as OLED displays, curved screens, and touch-sensitive interfaces contribute to consumer preferences.
B. Applications Across Industries
- Automotive and Aviation:
- Automotive: The automotive industry is witnessing a surge in demand for industrial LCD displays in various applications. Advanced infotainment systems, navigation displays, digital instrument clusters, and rear-seat entertainment systems are becoming standard features in modern vehicles. As autonomous driving technology evolves, the integration of sophisticated displays for augmented reality and enhanced driver information is expected to drive further demand.
- Aviation: In the aviation sector, industrial LCD displays are integral to cockpit instrumentation, in-flight entertainment systems, and mission-critical displays for military aircraft. The aviation industry’s focus on lightweight and energy-efficient displays, coupled with high-performance graphics, shapes the demand for specialized LCD panels to meet the stringent requirements of airborne applications.
- Automotive: The automotive industry is witnessing a surge in demand for industrial LCD displays in various applications. Advanced infotainment systems, navigation displays, digital instrument clusters, and rear-seat entertainment systems are becoming standard features in modern vehicles. As autonomous driving technology evolves, the integration of sophisticated displays for augmented reality and enhanced driver information is expected to drive further demand.
- Healthcare and Manufacturing:
- Healthcare: Industrial LCD displays play a vital role in medical imaging equipment, patient monitoring systems, and diagnostic displays in healthcare settings. The demand for displays with high resolution, accurate color reproduction, and 3D visualization capabilities is on the rise. The shift towards telemedicine and remote patient monitoring further emphasizes the importance of advanced display technologies in the healthcare sector.
- Manufacturing: LCD displays find extensive use in manufacturing environments for HMI systems, control panels, and industrial automation equipment. The displays are designed to withstand harsh conditions, including exposure to dust, moisture, and vibrations. The trend towards smart manufacturing, where data visualization and real-time monitoring are crucial, is driving the adoption of advanced LCD displays with touchscreen capabilities and Industry 4.0 integration.
- Healthcare: Industrial LCD displays play a vital role in medical imaging equipment, patient monitoring systems, and diagnostic displays in healthcare settings. The demand for displays with high resolution, accurate color reproduction, and 3D visualization capabilities is on the rise. The shift towards telemedicine and remote patient monitoring further emphasizes the importance of advanced display technologies in the healthcare sector.
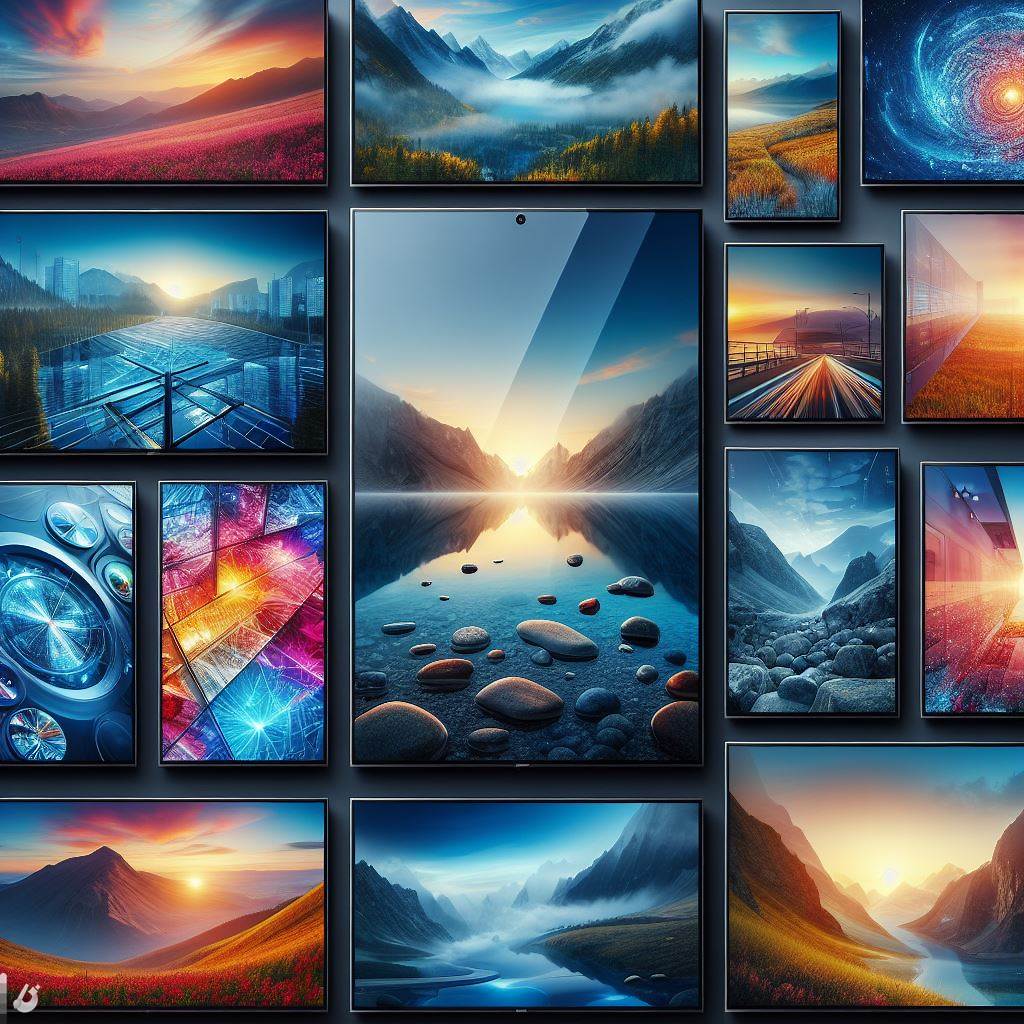
VII. Challenges and Solutions
A. Environmental Concerns
- E-waste and Recycling Initiatives: Challenge: The rapid advancement in technology, coupled with short product lifecycles, contributes to the growing issue of electronic waste (e-waste). Discarded LCD displays, containing materials such as glass, metals, and potentially hazardous substances, pose environmental challenges if not properly managed. Improper disposal can lead to soil and water contamination, posing risks to human health and the ecosystem.
Solution: Addressing e-waste involves implementing comprehensive recycling initiatives. Many countries and regions have established e-waste recycling programs to ensure the responsible disposal and recycling of electronic devices, including LCD displays. Manufacturers are encouraged to design products with recyclability in mind, facilitating the extraction of valuable materials and reducing the environmental impact of electronic waste. Collaboration between manufacturers, recyclers, and governmental bodies is essential to create effective e-waste management systems.
- Sustainable Manufacturing Practices: Challenge: The manufacturing process of LCD displays involves the use of various materials, energy, and resources, contributing to the industry’s environmental footprint. Traditional manufacturing practices may involve the use of energy-intensive processes, and the extraction of raw materials can lead to environmental degradation.
Solution: Sustainable manufacturing practices focus on minimizing the environmental impact throughout the entire product lifecycle. This includes adopting energy-efficient manufacturing processes, sourcing raw materials responsibly, and reducing waste generation. Manufacturers can implement eco-friendly initiatives such as using recycled materials in production, optimizing energy consumption, and adopting cleaner technologies. Certifications and standards, such as ISO 14001 for environmental management systems, can guide manufacturers in implementing and maintaining sustainable practices in their operations.
B. Social and Ethical Considerations
- Labor Practices: Challenge: Ensuring ethical labor practices throughout the supply chain is a significant challenge, particularly in regions where regulations may be lax. Labor exploitation, unsafe working conditions, and inadequate wages are concerns that need to be addressed to ensure the social responsibility of manufacturers.
Solution: Implementing and enforcing ethical labor practices involve transparency and accountability. Companies can conduct regular audits of their supply chains to ensure compliance with ethical labor standards. Collaboration with industry watchdogs, NGOs, and certification bodies can contribute to creating a framework that promotes fair labor practices. Transparent communication with consumers about the company’s commitment to ethical labor practices also fosters trust and encourages responsible consumer choices.
- Social Impact of Technology: Challenge: The deployment of industrial LCD displays, while contributing to technological advancements, can also have social implications. Job displacement due to automation and concerns related to the digital divide are issues that need to be addressed.
Solution: A holistic approach involves incorporating social impact assessments in the development and deployment of technology. Companies can invest in training programs to upskill workers affected by automation, fostering a smoother transition in the workforce. Engaging in community outreach programs, supporting education initiatives, and promoting digital inclusion contribute to mitigating the negative social impact of technological advancements.
C. Technological Challenges
- Rapid Technological Obsolescence: Challenge: The fast-paced evolution of technology leads to the rapid obsolescence of older display technologies, resulting in an increased rate of electronic waste.
Solution: Companies can adopt modular design approaches, making it easier to upgrade or replace specific components rather than entire devices. Additionally, promoting extended product lifecycles through firmware updates and providing incentives for device recycling can contribute to minimizing the impact of rapid technological obsolescence.
- Supply Chain Complexity: Challenge: The globalized nature of supply chains can introduce complexities, making it challenging to ensure ethical and sustainable practices throughout the entire chain.
Solution: Enhanced transparency and traceability within the supply chain can be achieved through the use of technology, such as blockchain, to monitor and verify the origin and journey of raw materials. Collaborative efforts between industry stakeholders, including manufacturers, suppliers, and regulatory bodies, can establish and enforce responsible supply chain practices.
- Overcoming Limitations in LCD Technology: Challenge: Despite their widespread use, LCD technology has certain limitations that have prompted ongoing research and development efforts to overcome these challenges. Some of these limitations include limited viewing angles, lower contrast ratios compared to other display technologies like OLED, and the inherent need for a backlight that can contribute to thicker displays and potential light leakage.
Solution:
- Advanced Panel Technologies: Manufacturers are investing in advanced panel technologies to enhance LCD performance. In-plane switching (IPS) and vertical alignment (VA) are examples of technologies designed to improve viewing angles and contrast ratios. These advancements contribute to better color accuracy and improved visibility from different perspectives.
- Mini-LED and Micro-LED Backlighting: The adoption of Mini-LED and Micro-LED backlighting is gaining momentum to address some of the challenges associated with traditional backlight technologies. These technologies offer improved local dimming, higher brightness levels, and greater energy efficiency, contributing to enhanced image quality and reduced thickness in certain applications.
- Addressing Issues Related to Product Lifespan: Challenge: The lifespan of LCD displays is a critical consideration, especially in industrial applications where continuous and reliable operation is essential. Over time, LCD displays can experience issues such as color degradation, backlight aging, and potential malfunctioning pixels, impacting overall performance and longevity.
Solution:
- Improved Materials and Manufacturing Processes: Utilizing high-quality materials and refining manufacturing processes contribute to prolonged product lifespan. Developments in materials science, including more durable glass substrates and improved liquid crystal formulations, aim to mitigate issues such as color shift and
degradation over time. - Enhanced Backlight Technologies: Innovations in backlight technologies, such as the adoption of organic materials or advancements in LED technology, contribute to improved backlight longevity. These enhancements aim to maintain consistent brightness levels throughout the display’s lifespan, reducing the impact of backlight aging on overall performance.
- Predictive Maintenance and Monitoring: Implementing predictive maintenance strategies involves utilizing sensors and monitoring systems to detect potential issues before they impact display performance. This allows for proactive measures, such as replacing aging components or addressing anomalies in a timely manner, to extend the overall lifespan of the display.
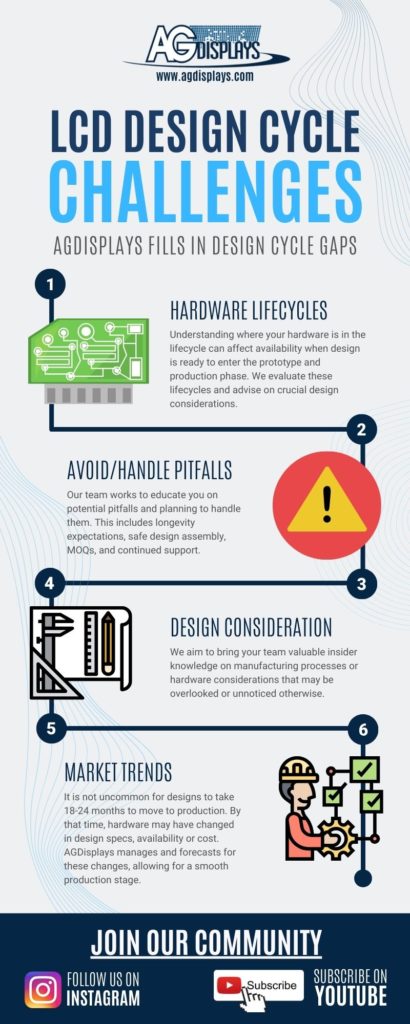
VIII. Consumer Integration
A. Integration of Industrial LCD Displays into Consumer Products
- Smart Homes and IoT Applications:
- Challenge and Solution: The integration of industrial LCD displays into smart homes and Internet of Things (IoT) applications presents challenges related to seamless connectivity, interoperability, and user experience. Manufacturers face the task of creating displays that can communicate effectively with a variety of IoT devices and platforms. Solutions involve the development of standardized communication protocols, such as Zigbee or Z-Wave, to ensure compatibility between devices. Additionally, user-friendly interfaces and intuitive control systems enhance the consumer experience, allowing for easy management of smart home devices through industrial LCD displays.
- Applications: Industrial LCD displays find applications in smart thermostats, home security systems, smart refrigerators, and other IoT-enabled devices within the smart home ecosystem. These displays provide users with real-time information, control options, and visual feedback, contributing to a more connected and efficient living environment.
- Challenge and Solution: The integration of industrial LCD displays into smart homes and Internet of Things (IoT) applications presents challenges related to seamless connectivity, interoperability, and user experience. Manufacturers face the task of creating displays that can communicate effectively with a variety of IoT devices and platforms. Solutions involve the development of standardized communication protocols, such as Zigbee or Z-Wave, to ensure compatibility between devices. Additionally, user-friendly interfaces and intuitive control systems enhance the consumer experience, allowing for easy management of smart home devices through industrial LCD displays.
- Consumer Electronics and Personal Devices:
- Challenge and Solution: The challenge in integrating industrial LCD displays into consumer electronics lies in achieving a balance between performance, energy efficiency, and form factor. Manufacturers need to deliver displays that offer high resolution, vibrant colors, and efficient power consumption. Solutions include advancements in display technology, such as OLED displays for enhanced color reproduction and flexibility, and improvements in power management to extend battery life in portable devices.
- Applications: Consumer electronics and personal devices, such as smartphones, tablets, laptops, and wearables, extensively utilize industrial LCD displays. These displays serve as the primary interface for users, providing them with a visually rich and interactive experience. The evolution of display technology, from traditional LCDs to OLEDs and AMOLEDs, has significantly enhanced the visual quality of consumer electronics.
- Challenge and Solution: The challenge in integrating industrial LCD displays into consumer electronics lies in achieving a balance between performance, energy efficiency, and form factor. Manufacturers need to deliver displays that offer high resolution, vibrant colors, and efficient power consumption. Solutions include advancements in display technology, such as OLED displays for enhanced color reproduction and flexibility, and improvements in power management to extend battery life in portable devices.
B. User Experience and Interface Design
- Impact of Display Quality on Consumer Satisfaction:
- Challenge: The quality of the display is a critical factor in determining user satisfaction. Challenges arise in ensuring consistent color accuracy, brightness, and contrast across different applications and usage scenarios. Achieving optimal display quality requires overcoming manufacturing variations, environmental factors, and the limitations of existing display technologies.
- Solution: Calibration technologies, advanced display processing algorithms, and quality control measures are employed to ensure that industrial LCD displays meet stringent performance standards. Continuous improvements in display technology, including innovations like high dynamic range (HDR) and wide color gamut (WCG), contribute to a more immersive and visually satisfying user experience.
- Challenge: The quality of the display is a critical factor in determining user satisfaction. Challenges arise in ensuring consistent color accuracy, brightness, and contrast across different applications and usage scenarios. Achieving optimal display quality requires overcoming manufacturing variations, environmental factors, and the limitations of existing display technologies.
- Trends in Touchscreen User Interfaces:
- Challenge: The demand for intuitive and responsive touchscreen interfaces presents challenges in terms of precision, durability, and user-friendly design. Touchscreen technology must evolve to meet the expectations of consumers for seamless interactions, multi-touch capabilities, and responsiveness across various applications.
- Solution: Ongoing research and development in touchscreen technology focus on improving touch sensitivity, reducing latency, and enhancing durability. Capacitive touchscreens have become standard in consumer devices, allowing for precise and multi-touch interactions. Emerging technologies such as haptic feedback, in-display fingerprint sensors, and gesture recognition contribute to innovative and user-friendly touchscreen interfaces.
- Applications: Touchscreen interfaces have become ubiquitous in consumer electronics, ranging from smartphones and tablets to interactive kiosks and automotive infotainment systems. The trend towards bezel-less designs and edge-to-edge displays further emphasizes the importance of responsive and aesthetically pleasing touchscreen interfaces in consumer products.
- Challenge: The demand for intuitive and responsive touchscreen interfaces presents challenges in terms of precision, durability, and user-friendly design. Touchscreen technology must evolve to meet the expectations of consumers for seamless interactions, multi-touch capabilities, and responsiveness across various applications.
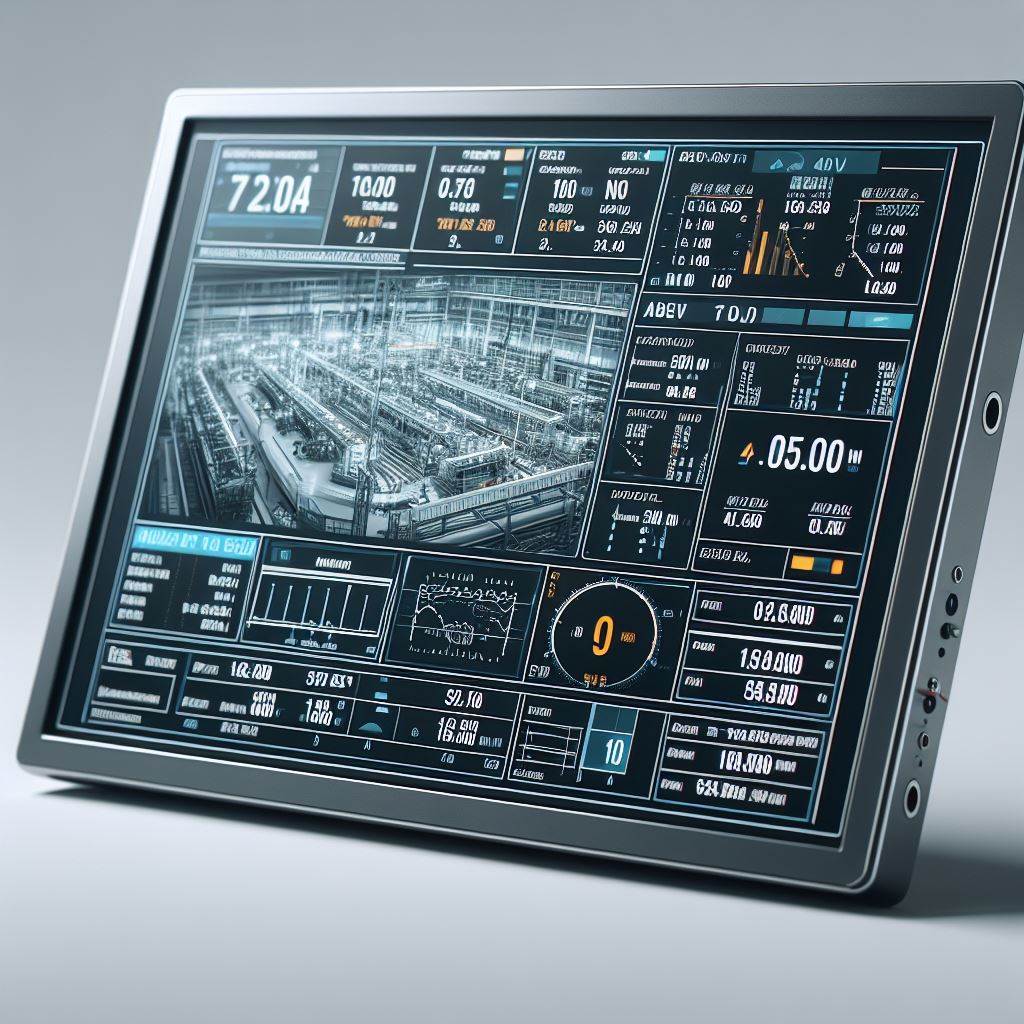
IX. Conclusion
A. Summary of Key Points
In this comprehensive exploration of the industrial LCD display industry, several key points have been highlighted:
- Industry Overview:
- The industrial LCD display industry plays a crucial role in providing visual interfaces for diverse applications across sectors, including manufacturing, healthcare, transportation, and more.
- The market has witnessed significant growth, driven by advancements in technology, automation, and the increasing demand for efficient data visualization.
- Manufacturing Process:
- The manufacturing process involves complex steps, from the selection of raw materials to the assembly and testing of LCD panels.
- Key materials such as glass substrates, liquid crystals, and advanced manufacturing processes contribute to the production of high-quality LCD displays.
- Factory Operations:
- Cleanroom environments, advanced technologies, and a skilled workforce are essential components of efficient factory operations in LCD manufacturing.
- Automation and data analytics play a pivotal role in optimizing production processes and ensuring high-quality outputs.
- Technological Innovations:
- Emerging technologies, including OLED displays and advances in touchscreen technology, are shaping the future of the industry.
- Industry 4.0 integration, marked by automation and data analytics, is enhancing efficiency and productivity in LCD display manufacturing.
- Supply Chain Management:
- Key players in the supply chain, such as LCD panel manufacturers and raw material suppliers, are vital for ensuring a stable and high-quality supply.
- Global distribution networks and challenges related to geopolitical factors require strategic planning for effective supply chain management.
- Market Trends and Consumer Demand:
- Growth projections indicate sustained expansion, with applications spanning automotive, healthcare, manufacturing, and more.
- Consumer integration of industrial LCD displays into smart homes, IoT applications, and consumer electronics is on the rise.
- Challenges and Solutions:
- Environmental concerns, social and ethical considerations, and technological challenges present challenges that require sustainable and innovative solutions.
- Overcoming limitations in LCD technology, addressing issues related to product lifespan, and adopting sustainable manufacturing practices are critical for industry advancement.
- Consumer Integration:
- The integration of industrial LCD displays into consumer products, including smart homes and IoT applications, presents challenges and opportunities.
- User experience and interface design, along with advancements in touchscreen technology, play a pivotal role in enhancing consumer satisfaction.
B. Future Outlook for the Industrial LCD Display Industry
The future outlook for the industrial LCD display industry is promising, with several trends shaping its trajectory:
- Continued Technological Advancements:
- Ongoing innovations in display technology, including the evolution of OLED displays, advancements in touchscreens, and the integration of more sustainable manufacturing practices, will contribute to the industry’s growth.
- Ongoing innovations in display technology, including the evolution of OLED displays, advancements in touchscreens, and the integration of more sustainable manufacturing practices, will contribute to the industry’s growth.
- Rise of Smart and Connected Devices:
- The increasing integration of industrial LCD displays into smart homes, IoT applications, and consumer electronics aligns with the broader trend of connected devices. The demand for seamless connectivity and enhanced user experiences will continue to drive advancements in display technology.
- The increasing integration of industrial LCD displays into smart homes, IoT applications, and consumer electronics aligns with the broader trend of connected devices. The demand for seamless connectivity and enhanced user experiences will continue to drive advancements in display technology.
- Focus on Sustainability:
- The industry will likely witness a continued emphasis on sustainable practices, from eco-friendly manufacturing processes to the development of displays with extended product lifespans. E-waste management and responsible supply chain practices will remain key considerations.
- The industry will likely witness a continued emphasis on sustainable practices, from eco-friendly manufacturing processes to the development of displays with extended product lifespans. E-waste management and responsible supply chain practices will remain key considerations.
- Adoption of Emerging Technologies:
- Emerging technologies, such as augmented reality (AR) and virtual reality (VR), may play a more significant role in the industrial LCD display industry. These technologies can offer new possibilities for immersive and interactive visual experiences in various applications.
- Emerging technologies, such as augmented reality (AR) and virtual reality (VR), may play a more significant role in the industrial LCD display industry. These technologies can offer new possibilities for immersive and interactive visual experiences in various applications.
- Rapid Evolution of Industry 4.0:
- The integration of Industry 4.0 principles, including automation, robotics, and data analytics, will continue to transform factory operations, leading to increased efficiency, reduced costs, and improved quality control in LCD manufacturing.
- The integration of Industry 4.0 principles, including automation, robotics, and data analytics, will continue to transform factory operations, leading to increased efficiency, reduced costs, and improved quality control in LCD manufacturing.
In conclusion, the industrial LCD display industry is poised for a dynamic future characterized by technological advancements, sustainable practices, and increased consumer integration. As the demand for high-quality displays continues to rise across various sectors, the industry’s ability to adapt to evolving trends and address challenges will be crucial for sustained success.